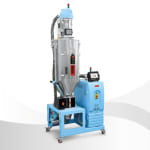
In today’s competitive plastics processing environment processors are always searching for ways to improve their processing capabilities. This ongoing search is geared towards equipment that allows for greater flexibility and fast production changes.
The Moretto Mobilux family of Mobile Drying and Conveying systems couple high-performance dehumidifying dryers, drying hoppers and conveying systems onto compact mobile carts that can be easily moved in and out of locations as needed. Unlike drying hoppers or complete drying systems that are mounted to the throat of a processing machine, the Mobilux Dryers include all necessary equipment for high-performance drying, yet can be moved where and when it is needed. Additionally, many processors find this mobility a convenient feature for prepping the dryer and pre-drying the resin in a non-production area, prior to moving the cart into a processing position.
A drying system designed for your specific requirement
Moretto offers two families of mobile drying systems for both higher and lower throughput processing needs.
The CRX Comb series of Mobilux Dryers is built around Moretto’s popular X Comb dryer. Each CRX Comb model includes a honeycomb wheel of 100% Zeolite desiccant, and is equipped with anti-stress technology preventing over-drying and automatic modulation of drying air for optimum drying performance with minimal energy consumption. Part of Moretto’s patented anti-stress technology is the manipulation of air flow to adapt to drying needs while maintaining a consistent drying quality. Only two parameters are needed, material type and throughput: all the rest is automatic! The dryer automatically manages all the other parameters such as residence time, process temperature, air flow and anti-stress. In this way, X Comb is able to apply the proper treatment for each type of polymer.
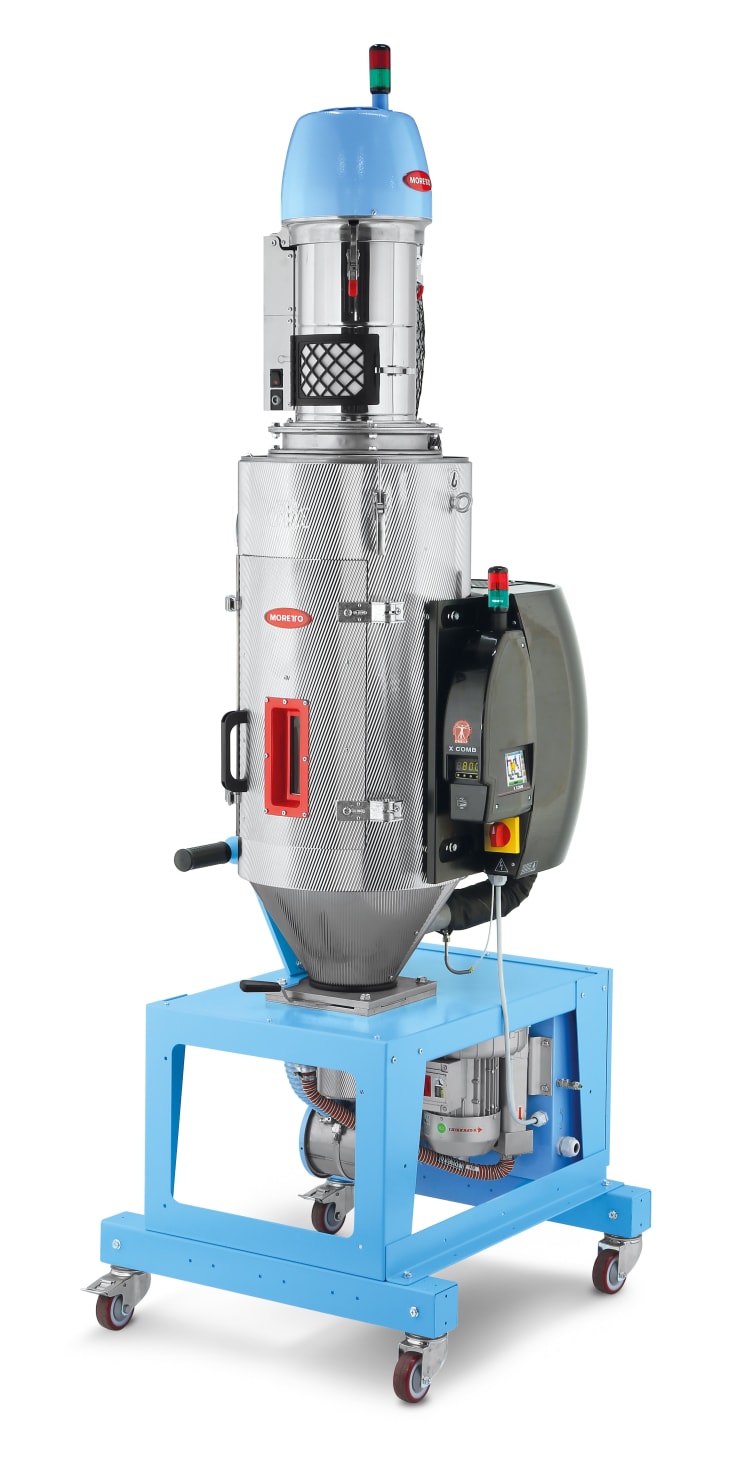
The technology behind the innovation
The use of exclusive Zeolite desiccant delivers continuous dew points of -60 °C and each CRX Comb requires only a single electrical power connection for operation; no compressed air or water is required, adding to the portability and convenience of the system.
Coupled to the X Comb dryer is Moretto’s unique OTX (Original Thermal eXchanger) hopper.
Also involving the university and engineering consultants alongside the company's R&D department, and through targeted investment, Moretto investigated the "hopper" issue. The company conducted a comprehensive analysis of the geometry, fluid dynamics and and thermodynamics of the system.
Moretto completely rethought the hopper, developing OTX, which revolutionized the dehumidification process and the concept of the hopper itself, realizing a real exchanger between energy and humidity, with extraordinary energy efficiency.
Drying time is reduced by 40% and, for the same throughput, the hopper volume decreases by 40%. In addition, thanks to the unique internal geometry and maximum attention to detail, energy efficiency is improved by 66%, significantly reducing the costs of such an energy-intensive process as dehumidification. Incredible results that represent a huge competitive advantage when compared to conventional hoppers!
The perfect control of the air flow eliminates variations in the material temperature at the mouth of the processing machine and, by significantly reducing the drying time, optimizes production changes.
In addition to the internal design, OTX features a patented external finishing, called Spyro. This unique stainless steel cover not only enhances the hopper's distinctive touch, but also increases its strength and makes it shockproof.
Evaluating the current electricity costs, this system guarantees a return on investment in less than two years. Its energy efficiency not only helps to protect the environment, but also to safeguard investors' portfolios.
