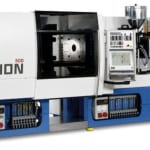
Netstal presents a trendsetting application in the area of multi-layer barrier compound and thereby rings in the next generation of plastic packaging products. A first example of this new, innovative packaging solution is made on the Netstal Elion, a moulding machine which is already perfectly established in the market.
Netstal shows on its Elion 500 a first example of a recently developed application from the area of „functional plastic packaging“. The moulded article is a container which - and this is the innovation - features a barrier foil between two injected layers of plastic. Thanks to this specific structure of the so-called multi-layer barrier compound the barrier foil is protected against damage from the outside on the one hand, and prevented from coming into contact with the product to be packed on the other. A further, not insignificant advantage is that this packaging product is also suitable for IML (In-Mould-Labelling). The same process lends itself also to the container lid.
The innovation resulted from the cooperation of the three partner companies Netstal-Maschinen AG and Glaroform AG of Switzerland, and Ilsemann Automation of Germany. The specialists of these three enterprises aim at replacing existing packaging products with barrier properties by high-grade reclosable plastic compound solutions which are produced efficiently and ecologically on the Elion 500 injection moulding machine. And it's on this Elion 500 that Netstal demonstrates the multi-layer barrier compound application at the Interpack to highlight also the economic efficiency of the all-electrically driven Elion range. The container in question is moulded at a cycle of less than ~6 seconds with a 1+1-cavity mould of the Glaroform company. Raw material feeding is by means of appliances of Messrs Motan of Germany.
The Elion guarantees a highly precise closed loop control of the moulding processes. This ensures not only highest product quality, but lowers the reject rate to an absolute minimum. The processor thus wins in two ways, apart from the economic benefits he makes a decisive contribution to preserving the environment and minimizing the carbon footprint of the production.
The demonstration of the system consisting of machine, mould, automation and further periphery - all ready for production - is a typical example of Netstal's know-how and experience in the supply of comprehensive solutions. The customer gets not only a highly productive injection moulding system, but also the processing knowledge enabling him to make parts of impeccable quality from the first hour of production onwards.