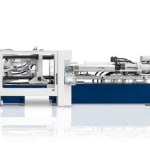
High speed with 450 and 750 tons of clamping force
A look back: At K 2016, Netstal presented the ELIOS 7500 to a global audience for the first time. "We are looking back at an extremely successful launch. Our customers from the packaging industry were extraordinarily interested in the ELIOS series. "In the first year, we were able to sell more than twice as many machines as originally projected," reports Netstal CEO Renzo Davatz. The Swiss injection molding machine manufacturer is now upping the ante by adding two smaller variants - featuring clamping forces of 4500 kN and 5500 kN - to the series. That means that within the series, customers can now choose between four main variants with clamping forces of 450, 550, 650 and 750 tons. Thanks to the innovative drive technology of the clamping unit, the smaller sister models are also the fastest machines in their respective class. For example, the ELIOS 4500 with a stroke of 574 mm achieves a dry cycle time of merely 1.5 seconds according to the Euromap norm. The ELIOS 5500 also convinces with a dynamic dry cycle of 1.7 seconds at a stroke of 644 mm.Top productivity and economic efficiency thanks to the hybrid drive concept for the clamping unit
"Manufacturers of thin-walled packaging know that the shortest cycle times coupled with top availability and quality are the keys to an effective reduction of unit costs. That has been our guiding principle during the development of the entire series," Davatz explains. The 5-point dual toggle lever, which is moved via a central crosshead with drive elements that act simultaneously, is the heart of the machine. A dual toothed-rack drive with a highly dynamic, water-cooled servo motor is used for the purely electrical movements. Two synchronous cylinders, which feature a parallel alignment, assist with building up the full clamping force. "This concept offers many advantages, because the small mass moment of inertia of the motor allows high acceleration values and dynamic movements of the clamping plate. At the same time, the plate is moved very harmoniously while the mold position is controlled with great precision and in a way that is gentle on the mold," Davatz explains. Thanks to the optimized toggle lever geometry, the clamping unit of the ELIOS is particularly energy efficient and offers ideal conditions for the recovery of the movement energy. The kinetic energy generated during braking processes flows into the electric motor of the main drive where it is converted into hydraulic energy and stored. That is why, compared to conventional designs, an ELIOS requires approximately 50% less energy.ELIOS series machines are designed for top packaging application productivity