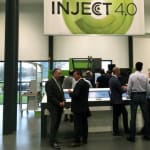
“As the most recent staging proves, ENGEL’s med.con is now an established networking event for plastics processing firms in the medical technology sector,” says a delighted Christopher Vitz, Managing Director of ENGEL Deutschland in Hannover, commenting on the high levels of interest shown by participants. The event in Hannover did not only attract medical technology experts from the subsidiary's sales area, but also from the surrounding regions. “Our customers and partners use this platform to learn and exchange information about trends as well as innovative products and processes,” confirms Christoph Lhota, Vice President of ENGEL’s medical business unit. “Feedback from participants has been very good, especially as many of the ideas are suitable for immediate, practical implementation."
Early interdisciplinary collaboration the key to success
The presentations focused on requirements, trends, innovative products, the opportunities of digitalisation and, above all, integrated system solutions: close cooperation between all organisations at an early project stage is increasingly becoming a success factor. Only where all components - from raw material to mould, injection moulding machine, automation, peripherals and processing technology - are precisely coordinated from the outset is it possible to maximise quality and efficiency potential, and make adjustments to product design as necessary. The examples on show illustrated this point. In one current project, for example, the number of plastic components in an inhaler was reduced from the original draft design, thereby removing the need for several work steps and moulds and reducing project costs significantly.To deliver system solutions customised to the specific needs of processing firms from a single source, ENGEL works closely with partner companies. A number of these attended the event as speakers, including IGS Gebo Jagema from the Netherlands and Hekuma from Eching in Germany. Professor Dr. Thomas Seul, Pro-Rector for Research and Transfer at Schmalkalden University of Applied Sciences and president of the Association of German Tool and Moldmakers (VDWF), opened the conference with a keynote address. A personal report with a strongly practical focus was then delivered by Dr. Jochen Heinz of Transcoject; the family-run company based in Neumünster produces pharmaceutical packaging and application systems for human, dental and veterinary medicine, including highly complex prefillable syringes of cyclic polyolefins.