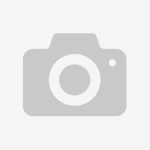
- The shorter moulding cycles achieved with Crastin SF can deliver cost savings ranging up to 20 percent - said Dave Donofrio, global business manager for Crastin at DuPont Engineering Polymers. - The super-fast moulding resins are particularly advantageous in moulding thin-wall parts such as connectors and large parts such as structural housings.
The key to the cycle time reductions provided by the new resins is their exceptionally high flow. For example, the melt viscosity of a 30 percent glass Crastin SF grade is 43 percent lower than that of a comparable standard grade at 250°C and a typical moulding process shear rate of 1000 s-1.
The high flow of Crastin? SF grades opens the way for major reductions in melt
temperature, thus saving precious seconds in the duration of hold pressure and cooling. The chart above shows a typical example. In addition to reducing cycle time, the enhanced flow of Crastin SF resins can also enable the design and production of parts with thinner walls.
For large parts, this can lead to substantial savings in material consumption and part weight. In the case of small parts, it can permit new part designs with longer, more intricate flow paths. The higher flow of Crastin SF resins also opens the way to cost savings through the use of moulds with more cavities. Alternatively, because Crastin SF requires lower injection pressure, the moulder can employ a smaller machine, which costs less to buy and to operate.
The mechanical properties of the new resins are very similar to those of comparable standard grades, according to Donofrio. - We achieve that impressive result with new technology that enhances the flow of polymer chains at the molecular level while maintaining the properties expected for comparable PBT resins - he said.