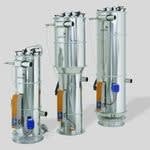
The Metro P (the P stands for powder) hopper loaders have been developed specifically for the safe and clean 24/7 continuous operation, requiring very little maintenance when conveying both non-free-flowing (type N) and free-flowing (type F) raw materials. To achieve this, the systems – as integral units within the motan product range – are equipped with the well proven mechanical and control-specific interfaces.
To refill the 15/25/50 litre units, the discharge flap activates the vacuum valve via a signal. The reason for the success of the complete process reliability lies in the fact that the forming of lumps and bridging are thus impossible. The geometries of the discharge flaps – as calculated computationally, empirically and under laboratory conditions – guarantee sustainable reliability. The largest of the units, achieving an output of 1000 kg/h, has a flow-opening with a diameter of 260 mm.
The series Metro P is available in three sizes for the proven applications: the compact unit with an output of 200 kg/h and a capacity of 10 litres (cycle), the mid-size unit with an output of 500 kg/h and a capacity of 25 litres, and the “Big Fellow” with an output of 1000 kg/h at a capacity of 50 litres. Classifications F for free-flowing powder and N for non-free-flowing raw materials apply to all three unit sizes. The tall, slim cylindrical containers are produced in electro-polished stainless steel and are thus per se robust, extremely durable and easy to service.
Filter quality is the beginning and the end in this process technology. The conveying of powder substances and substrates demands the employment of micro filters in the environs of the conveyor air. For the Metro P units, motan employs multiple filter cartridges. These star-filters are characterised by an extremely large surface area and their Teflon-coating, whereby most minute and the finest powder particles in the µ-range are able to be ‘captured’, gathered and filtered out.
With the compact Metro P – output 200 kg/h, volume 10 litres – a battery of four filter cartridges is deployed. For the mid-size unit – output 500 kg/h, volume 25 litres – as well as the largest unit – output 1000 kg/h, volume 50 litres – seven filter cartridges are used respectively.
Cleanliness, safe maintenance and care of the equipment in the Metro P range of products are further enhanced by motan’s decision to deploy automatic air-jet de-dusting during both the operation and the conveying process. Within a defined sequence schedule, the air-jet return current is thus pneumatically unloading the predestined cartridges, i.e. either sets of four or seven – selectively or sequentially triggered just about one second before the end of the conveying cycle.