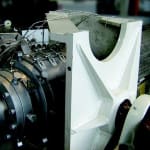
After the leading Polish pipe manufacturer had tested the prototype of the spider 200-3 die for six months, they decided to buy it because of the enormous benefits.
“We have now been using the new die in regular production for three months and are extremely satisfied with the significant advantages compared to the feedblock-die combination we used previously. Its easy handling attributes together with optimal pipe quality are particularly impressive”, Robert Stasiak, Managing Director of InstalPlast sums up.
InstalPlast has been using the new die to produce 3-layer foam core pipes ranging from 32 to 200 mm in diameter on an existing co-extrusion line. In this line with its two reliable parallel twin-screw extruders from battenfeld-cincinnati, the new spider 200-3 die has replaced the feedblock-and-standard-die combination used previously.
The design of the new die is really something out of the ordinary. Regardless of their viscosity, the two melts for the inner and middle layers are both fed into it centrally via a newly developed distribution system. In contrast to conventional dies, where the melt for only one layer could be fed in centrally, this is now possible for two layers for the very first time. Only the melt for the outer layer is fed in laterally via a side-fed distributor laid out as a coat-hanger model. To compensate for differences in viscosity, the outer layer can be centered separately from the other layers of melt.
This design yields five major benefits for pipe production:
Thanks to the smaller number of components, this die is much more compact and easier to handle. This also simplifies setting up and cleaning of the die.
The fact that this die requires less work for setting up facilitates the start-up procedure. “Thanks to the shorter start-up times we have been able to halve the length of start-up scrap pipe”, Stasiak is pleased to note.
This optimized pipe die design enables significantly improved wall thickness distribution in multi-layer pipe production and thus material savings. InstalPlast has achieved a consistent, even wall thickness distribution with a 20 % increase in throughput. At the same time it was possible to reduce the weight per meter of the pipes permanently by 5%.
The resulting higher process stability is another benefit.
Finally, the spider 200-3 die also scores with more favorable process conditions, since less pressure is built up inside the die.
InstalPlast is well known as one of the leading pipe manufacturers in Poland. In 2010, the plastics processor produced some 20,000 tons of pipe from PP, PVC and HDPE for a great variety of water conduit systems. The company was established in 1991.
Its product range comprises infrastructure capital goods, for example for expressways, sewerage systems, road drainage, complete fresh water and waste water conduit systems for parking lots, garages and industrial buildings, as well as residential, office and service buildings such as restaurants and retail stores.