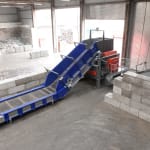
Baling wire is essential in the recycling industry: without it, it would be far more difficult to collect, transport and handle the large amounts of waste materials that enter the recycling process. However, the extensive use of wire means that recycling facilities face the challenge of dewiring the bales efficiently and safely.
“It is a complex task, which is usually done manually or with limited mechanical assistance,” explains Rok Mežič, Head of Development at Stadler. “However, manual removal is time-consuming and labour-intensive, and poses safety risks for workers. In our sorting plant projects and speaking with our customers, we saw that this was a significant pain point in the existing process and decided to develop a solution to address the issue efficiently. The result is our new WireX, which fully automates the process, dewiring bales in a single pass. It significantly increases the efficiency of the process and the sorting line’s capacity, as well as improves workers safety. We believe that WireX fills a critical gap in the market, aligning closely with our customers’ needs and setting new industry standards.”
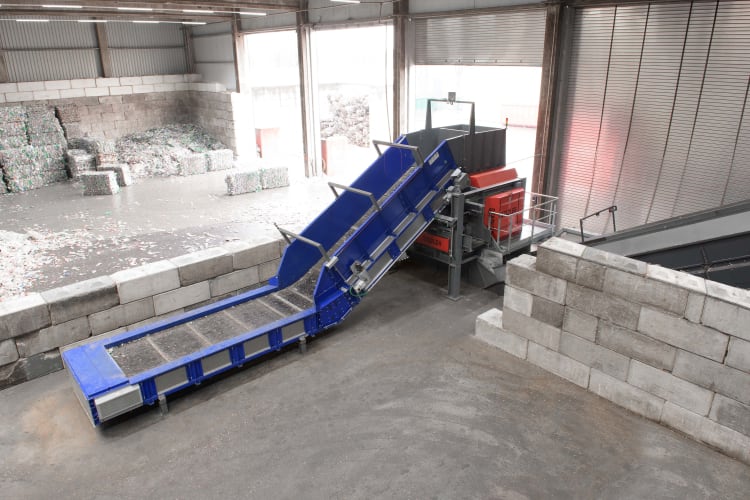
An industry first: dewiring crosswired bales in one pass
Using sensor detection and measurement systems, the new Stadler Wirex effortlessly measures the bales and removes the wires from single- and cross-wired bales in one pass without double feeding. The steel dewiring unit is integrated into a steel frame resistant to vibration, also made of steel. The machine geometry is designed for standard bale dimensions to ensure smooth operation.
The bales are fed onto the machine by an independent conveyor, guided by a moving push plate onto the floor plate, which keeps the bale in position. Sensors located above the input conveyor, inside the chamber and on the flap ensure the bale is positioned correctly with high precision. Once the bale is in position, combs are pushed into the bale to fix the wire for cutting. The bale measurement system ensures the cutters move in the bale correctly. When the cutting is done, the combs pull out and the wires are coiled up and discharged by a small integrated conveyor into a separate bin, ready for recycling. The floor plate opens and the bale falls onto a conveyor placed below the machine, which will feed the material into the sorting system.
“With WireX the bales are dewired quickly and efficiently, saving considerable time as there is no need for a second pass of the bale or manual intervention to remove all the wire,” says Rok Mežič.
The new WireX has followed STADLER’s rigorous development and validation process and has been extensively tested at STADLER’s test center in Slovenia. It is also in the final stages of further testing in real conditions at a customer’s recycling facility.
Interested customers can see the new WireX in this video