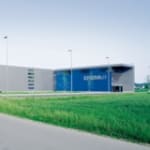
Since it was founded in 1983, EREMA has specialised in the development of plastic recycling technologies and revolutionised the industry again and again with numerous innovations. EREMA technologies have now been regarded as the leading global standard for a wide variety of recycling applications for decades. The heart of the EREMA systems is formed by the large patented cutter/compactor and extruder combination which can be used for a wide variety of recycling jobs according to the configuration in both inhouse production waste recycling and severely contaminated post-consumer waste applications.
EREMA managed the major breakthrough with the first generation of systems launched in 1983, the year it was founded. EREMA combined for the first time ever a cutter/compactor with a - back then still radial - extruder and thus made it first possible to cut, compact and extrude waste plastic in a single, continuous process. The machines were straightforward to operate, had low space requirements and consumed on average 30% less energy compared to the industry standard at that time. Major importance was attached to this new technology for the economic recycling of thermoplastics within a very short time.
EREMA continued to develop this technology and with the launch of the second plant generation in 1993 once again brought about an advancement in the industry on a large and almost dramatic scale. Thanks to the extruder now being located tangentially to the cutter/compactor, EREMA was able to enhance the quality of the end products enormously while increasing output and performance considerably, too. Additionally, a newly defined and optimised scaling of the cutter/compactor in relation to the screw diameter of the extruder connected (patented) made feeding even easier with very large individual portions. Project-oriented modifications to the cutting tools in the cutter/compactor also helped to optimise this process. The longer dwell times in the big cutter/compactor were a further benefit of this innovative technology, making it possible to direct the material to the extruder with much more homogeneous temperature distribution.