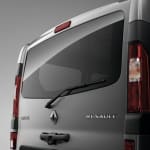
Ichikoh Japan wanted a processing solution that could achieve good appearance at the welding areas on plastic parts. However, this would be impossible to achieve with conventional welding techniques such as hot plating or vibration welding due to complicated part designs and shapes. For this reason, a new laser welding technique was utilized for the rear lamp housing to facilitate more design freedom and achieve the required surface appearance. In addition, this new laser welding technique also has the potential to generate more stability and higher mechanical strength at welded areas compared to conventional welding methods.
The challenge with most black or dark colored polymers is the materials' high sensitivity to laser beam, resulting in uneven surfaces at the welding area when a laser beam is applied. As such, Ichikoh sought to find a polymer solution that would not only optimize the process to achieve suitable laser welding conditions but would also adhere to the substrate and most importantly, a great looking finished product. Ichikoh partnered with Ineos Styrolution to select the right styrenic polymer for the application. Working in collaborative innovation, Ineos Styrolution custom developed Novodur HH-112, a high-heat ABS specialty styrenic grade that would offer the performance and aesthetic qualities they require. This marks the first time an ABS resin has been used for a black color laser welded application.
In the end, the leading Japanese car manufacturer was pleased with the vastly improved part appearance at the welding area. The new process and polymer solution also helped the car manufacturer improve the quality of their cars design.
Novodur high-heat ABS grades meet stringent stability requirements for thermally stressed components. Novodur high heat is the material of choice for numerous heat-resistant applications, like rear lamp housings, radiator and front grilles, as well as exterior trims. The new Novodur HH-112 product is now available globally from Ineos Styrolution.