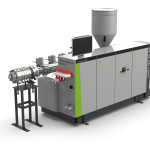
One of this year’s highlights at the battenfeld-cincinnati trade fair booth is the new helix II 32-5 VSI 5-layer pipe die which recommends itself by easy handling and extremely short flushing times. It is being presented at booth No. B19 in hall 16 not only in combination with the new solEX 45NG single screw extruder, but also set up in a clearly visible way, so that every visitor gets a chance to take a close-up look at the design of the flow channels and the melt distribution system.
The pipe die on display belongs to the latest generation of helix pipe dies, by which battenfeld-cincinnati shows once more how mechanical engineering expertise can master the challenge of changing market and customer demands. Easy handling and minimization of material losses were top-priority goals in developing this new product line, and these goals have been achieved by intelligent action.
Every pipe die normally needs to be taken apart and cleaned from time to time. Especially for smaller multi-layer dies, this may quite often become necessary. Sometimes, the materials to be processed are changed at short intervals, or the materials tend to form deposits. In such cases, easy handling of the equipment is vital. This aspect was taken into account by various measures in the development of the new pipe die. Firstly, the number of individual components has been reduced, and secondly, virtually all components are centered via a cone, which ensures maximum user friendliness and prevention of faults.
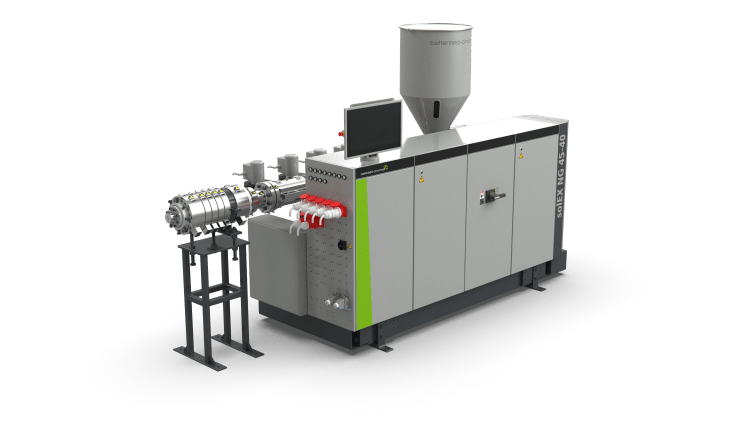
Another focus lay on optimizing the flow channels. The objective here was to minimize the flushing times, in order to make the changeover processes as efficient as possible. A simultaneous target was to ensure high precision in layer distribution across the entire circumference of the pipe.
All of this could be achieved by combining melt distributors of several different designs, which were optimally harmonized with each other. In this way, the average residence time, a good indicator of the flushing time to be expected, was reduced by more than 50%.
The helix II 32-5 VSI exhibited at the K is designed for PE pipes with external diameters ranging from 6 to 32 mm with an output of 350 kg/h. The entire pipe die series with the proven spiral mandrel, a spiral distributor combined with a lattice basket, comes in 15 different s. It covers pipe dimensions ranging from 4 mm to 3,000 mm and possible outputs from 300 to 3,000 kg/h.