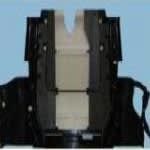
When choosing an absorber system, outstanding insulating and mechanical material properties play a decisive role for the manufacturers, but increasingly often so does available space. Sekisui Alveo, manufacturer of polyolefin foams, has optimized the acoustic properties of its products through modification and special treatment. The new flat absorber made of micro-perforated Alveocel foam efficiently reduces noise emissions in the engine compartment and meets the need of the automobile industry for space-saving solutions.
Already for years, Sekisui Alveo has been closely collaborating with systems suppliers to develop various efficient box absorber solutions. Due to the thermal requirements, only highly resistant PP foams come into question for applications in the engine compartment - foams that possess extended temperature resistance of over 140°C. With its new foam Alveocel, the company has now developed an especially space-saving variant: a flat absorber made of micro-perforated foam.
Perforation instead of thermoforming. The Alveocel foam is needled in a specific pattern and thereby is given its acoustical function. The acoustic waves penetrate the partially open cells after perforation. There they are on one hand transformed into kinetic energy (Helmholtz resonance effect), and on the other into heat energy by friction (dissipation). Through the combination of the two effects, the flat absorber covers a wide frequency range.
Even a single-layer micro-perforated absorber efficiently reduces noise emissions from the engine compartment. The absorptive effect is increased by the use of several foam layers.