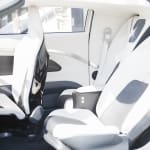
What does the user expect from the future automotive interior? With shared, autonomous cars being the main symbol for future mobility, the interior as we know it today will undergo a profound change. The steering wheel will disappear, the passengers will not have to focus on the traffic anymore. Seats, which now allow only position adjustments will be able to turn around completely. Roof and side windows will be bigger, to make the cabin brighter and to allow the passengers to enjoy the landscape surrounding them. With more time at hand, passengers will ask for more displays, audio systems, more entertainment features in general – but also for peace and quietness. To put it short: The automotive interior of the future is going to become a space of comfort and relaxation – a new living space. But these new expectations are challenging the car manufacturers, since every additional feature will add to the overall weight of the car.
Lightweight materials will significantly add to the vehicle of the future. From the manufacturer’s point of view lightweight materials are first and foremost a key factor to achieve the CO2 fleet emission goals. At the same time, they contribute to a better range or fuel efficiency – without compromising safety. To reduce weight not only metals can be replaced, also existing plastic applications can be downsized and redesigned by using newly developed or improved thermoplastics.
From the user’s point of view lightweight itself is no emotional experience. Especially when used in the interior of the car, human senses come into play. The materials should not smell, appeal to the eye and – due to the rising popularity of car sharing – also withstand intense use by many different users. With the automotive interior becoming a living space, the materials should also be able to reduce noise coming from outside the car. At the same time noise from inside the car should stay inside.
Consequently, how can plastics and foams help to meet these expectations? Asahi Kasei offers a diversified range of materials which can bring the future automotive interior to life.
Tenactm Polyacetal (POM) – Can you smell the difference?
The in-cabin air quality is becoming increasingly important. With the increased use of plastics inside the car, the reduction of VOCs (volatile organic compounds) is becoming a key factor for an improved in-car air quality. VOCs are carbon-based gases that can evaporate from plastic materials into the air at room temperature, especially in newly produced cars. In closed environments, these gases can lead to discomfort and health issues, such as headaches or nausea.
Asahi Kasei, the world’s only manufacturer of homo- and copolymer POM under the brand name Tenactm developed a low-VOC material many years before the automotive industry started to address this issue. Tenactm has the world’s lowest VOC emission class – exceeding the high standards of all OEMs worldwide. In addition, properties like low friction, scratch resistance and a high mechanical strength make Tenactm a suitable material for applications in the automotive. It is already used in applications like sliders for seat adjustments, lumbar support for seating comfort, or seat belt push buttons. The company has recently developed a metal-looking low-VOC Tenactm, using aluminium flakes as a filler. Looking and feeling like metal, it features a high scratch resistance while at the same time improving the in-car air quality compared to other materials.
Thermylene Polypropylene (PP) - The economic alternative
The economic alternative Considering the concept of autonomous vehicles, panoramic roofs allow more light inside and offer excellent views of the surrounding to the passengers. Asahi Kasei’s glass-reinforced polypropylene Thermylene® features a high flowability and offers cost advantages compared to polyamide. Lighter and larger sunroof panels made of this material will add to the overall living-space experience of the future automotive.
Leonatm Polyamide (PP) - Looks good, lasts long
Looks good, lasts long With more sunlight inside the car, the necessity for UV-resistant materials will grow. Asahi Kasei’s semi-aromatic glass-filled polyamide Leonatm withstands the toughest automotive exterior UV tests – without any additional coating. It is used for exterior mirror brackets – and is now finding its way inside the car. It is already used for the fine thin-walled and unpainted blades of a dashboard venting system, directly positioned under the front windshield and with maximum sunlight exposure.
Polyamide Foam (under development) - The sound of silence
The sound of silence Sound insulation will become a key factor for the living-space experience inside the car. Ambient noise will need to be kept outside, while loud music should stay inside the car. Based on its expertise as one of only four fully integrated polyamide manufacturers Asahi Kasei is currently developing the world’s first polyamide bead foam. Featuring the proven properties of polyamide – like high heat and chemical resistance – the special C- or macaroni shape of its beads also enable a significant noise reduction.
At the K 2019 Preview in Düsseldorf last week, the company presented its vision of the future in-car living space.
Source: Asahi