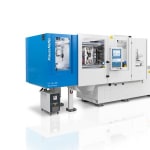
Better injection molding productivity can often only be achieved with lots of small steps which add up to create a great effect. Under the exhibition motto "Productivity Plus", KraussMaffei is exhibiting small and medium-sized injection molding machines at the Fakuma (Hall A7/Booth 7303), illustrating how intelligent plasticizing, control and automation solutions can improve productivity. The focus of the exhibition is applications using the new hydraulic CX series and the all-electric AX SilcoSet for processing liquid silicone rubber.
Conserving energy and resources
"Resources are limited and raw materials are becoming ever more expensive. That makes reducing the amount of energy, oil and material we use worthwhile in the long run. That is why, for example, the drive concept of the new CX has been energy-optimized, giving the machine an intelligent memory management system needing ten percent less power," explains Dr. Hans Ulrich Golz, Managing Director of KraussMaffei and President of the Injection Molding Machinery segment of the KraussMaffei Group. Further significant savings potential can be found in the new machine function APC (adaptive process control), which allows the injection molding machine to restart quickly and to process even difficult batches of material with high proportions of recycled materials into premium quality components. Further savings potential can be found in the excellent homogenization of the HPS screw, which enables, for example, the color master batch proportion to be reduced by up to 30 percent.
From matt to high-gloss
Exciting surface effects with laser and hologram look are being created at the Fakuma on a CX 160. This is made possible, for example by a dynamically inductive mold temperature control system (Dynamic Mold Heating - DMH) from RocTool and with the tooling expertise of Roctooling. The molds have special surfaces with different effects (matt, high-gloss, with punched holes), impressively demonstrating the design options for premium quality visible components. "DMH is an excellent example of production efficiency. There is no need for additional film technology," explains Jochen Mitzler, head of Strategic Product Management at KraussMaffei. Like all KraussMaffei exhibits, the CX 160 is equipped with the new, intuitively operated MC6 Multitouch control system, which enables all injection molding machines and automation components to be centrally controlled. With a 24-inch monitor, even complex processes can be executed with gestures and swipes. The SlideX guide track ground into the glass enables the operator to control the movements of the machine without having to look.
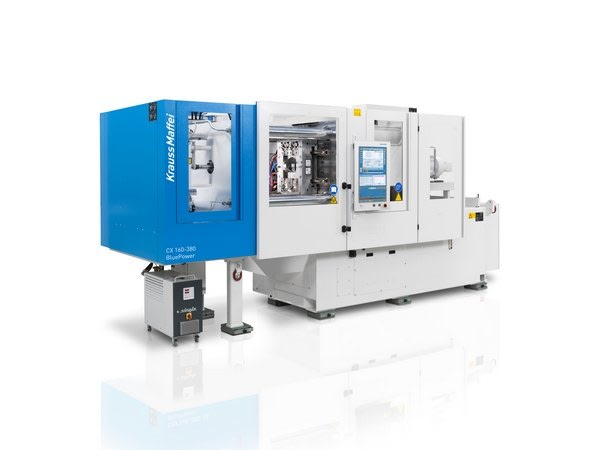
40 percent weight reduction with FiberForm
The FiberForm process developed by KraussMaffei combines injection molding with thermoforming of composite sheets to further improve the strength of fiber-reinforced plastics. As a result, the combination of lightweight materials and design in the construction enables new fiberreinforced thermoplastic components to be manufactured with particularly high strengths. At the Fakuma, a CX 300 is producing airbag housings in cycle times of 42 seconds. "The FiberForm process makes an important contribution to lightweight construction suitable for series production with thermoplastic fiber-reinforced plastics. Compared to conventional metal components, these represent a weight saving of around 40 percent," Mitzler explains. In this process, endless-fiber fabric or textiles impregnated with a thermoplastic matrix are heated, then shaped in the injection mold and finally overmolded. Like injection molding, the FiberForm process is easy to automate and can be used in fully automated production with compact manufacturing cells. The exhibit at the Fakuma is equipped with an LRX linear robot of the TwinZ version. The multiple kinematic system is compactly integrated into the standard housing. Partners for the exhibit include the companies Takata and Christian Karl Siebenwurst.
Silicone - a true all-rounder
Silicone is on the rise, in the form of liquid silicone rubber (LSR) or of solid silicone (HTV - High Temperature Vulcanizing). In particular medical technology and the automotive and leisure industries are increasingly interested in the outstanding physical and chemical properties of the material. At the Fakuma, KraussMaffei is demonstrating the production of a nasal ventilator made of liquid silicone rubber. The product runs on an allelectric AX with 500 kN clamping force in a four-piece mold. The SPX 10 sprue picker with extended function takes the parts, separates them and deposits them. The Elmet metering and mixing unit provides for optimum draining of residual fluids, ensuring that no material goes to waste. The AX SilcoSet is suitable for use in cleanrooms and is approved for medical use. All-electric AX series injection molding machines from KraussMaffei feature resource-efficient manufacturing with high repeatability. They earn a rating of Class 9+ on energy efficiency tests.