Craft Line: Paper for a natural shopping experience
Thanks to their combination of sustainability and branding, Südpack’s new film packaging solutions with paper component are another highlight at FachPack. The products Veraplex Craft, Ecocraft Skin and Ecocraft Shape form the new Südpack Craft Line, which is characterized by its nature-inspired look and feel, and good printability. All solutions combine a thin layer of plastic with paper – and undiminished performance. FachPack visitors can get to know the new bottom film Ecocraft Shape, which is particularly flexible. It is made of 80 percent paper and a thin layer of PE, on the side that comes in contact with the product. This approach saves plastic, while also making it possible to flexibly adapt the packaging to the product: the Ecocraft Shape can be deep drawn up to 15 millimeters and offers packaging with an appealing look and feel, especially for cheese, sausage and meat products. In turn, after product consumption, the Ecocraft Skin allows the cardboard and film to be easily separated: clear and simple recycling tips provided on the packaging, and easy-to-separate materials make properly sorting waste quick and easy.
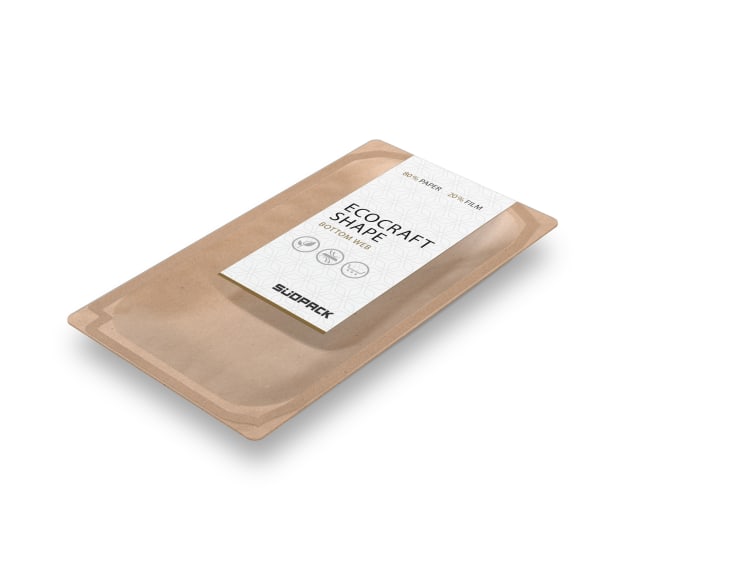
The new bottom film Ecocraft Shape is made of 80 percent paper and a thin layer of PE. It can be deep drawn up to 15 millimeters and offers an appealing look and feel, especially for cheese, sausage and meat products.
Recycle and replace: keeping the entire supply chain in mind
Südpack is not only focused on using more and more recyclable plastic. Many plastics used in film manufacturing already are recycled or internally regranulated. “Plastic is a valuable raw material. That’s why, whenever possible, we use recycled material for our films,” says Johannes Remmele. “Needless to say, in this regard quality, product protection, and hygiene remain our topmost priorities.” Thanks to the founding of their in-house compounding center in Schwendi, Südpack will soon be able to produce its own plastic granulates. By mixing and manufacturing its own granulates, the company will be able to more precisely tailor their characteristics, and to accelerate the development process for new products. Here, one focus area will concern the treatment and further processing of secondary raw materials generated during production so as to yield regranulates. In turn, Südpack will use the regranulates for its own products, creating a closed material circuit.
Moreover, all products and processes at Südpack are being continually refined and improved: “Respect and innovation are the keys to improved sustainability,” claims Carolin Grimbacher. “That’s why we’re investing heavily in new technologies and techniques that will make our products even better and more sustainable.” For example, the testing facility multiXtrusion allows the experts at Südpack to simulate all conventional manufacturing techniques for plastic films, and to identify how they could be optimized. This approach yields e.g. particularly resource-efficient films, which can also be brought to market sooner. Südpack is also at the forefront of developing new, innovative technologies for the recycling of composite plastic films: as a partner in BASF’s pilot project “ChemCycling,” the film experts recently produced the world’s first prototype package made completely of chemically recycled plastic – an important milestone on the road to 100% recyclability, even for composite films.
Source: Südpack