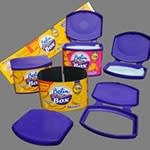
As a start-up company Wallbox has managed to interest its customer LU with its new concept of producing a box with a plastic bottom and a re-closable plastic cap on top. Being the manufacturer of the packaging concept Wallbox needed additional expertise in plastics processing and mould technology to be able to deliver the appealing looks and quality that LU was looking for. At an early stage Stork Plastics Machinery was approached to take part in the project to help find the optimal solution to produce the bottom and the top of the box.
After the initial discussions the Belgian toolmaker Loomans was introduced to participate in the design, engineering and delivery of the moulds. By doing so, Wallbox is able not only to design the box according its customers specification, but also to supply the body, top and bottom of the box to its customer. Furthermore Wallbox delivers the machinery to assemble and fill the boxes on the customer's site. Today, at Wallbox, new Stork S+ 250t machines are installed to produce the first 9,000,000 boxes planned for 2009. The machines are producing with 2+2 stack moulds from Loomans.
Wallbox has developed the new and very flexible concept for packaging dry goods into a box with exceptional properties. The operating principle has been patented as NewCaps Technology, and Wallbox developed the packaging machine to implement this great idea. The machine consists of a staged process, where the boxes are assembled and filled with contents in a vertical manor during eight process steps maximum.
This concept speeds up the packaging process and it's flexible. The machine can be re-adjusted within minutes to allow short set-up times for special variants of the same product. This feature is used for instance to produce extra promotional products, because these often require a different size, extra contents or an extra gadget for marketing purposes. The packaging machine can handle boxes up to 28 cm high. The machine is flexible and can be equipped with different tools to allow the creation of distinct shapes and sizes of boxes. La box LU Belin modulair.
The machine assembles and fills the box in eight stages. The bottom, top and body are shipped to the costumer by Wallbox. The top has a cap and is already sealed. The components are fed into the assembling and filling machine on the customer's site. First the body of the box is formed into the right shape, then both ends of the body are fused together to get an air tight weld. After that the body is placed and glued onto the plastic bottom of the box. Steps 4, 5 and 6 can be used to fill the box with the required contents. Finally the plastic top, is glued onto the box and the final result is checked by the machine with a vision system.
Producers of packaging products are confronted with lots of market and customer demands. Moreover, they have to consider the environmental issues as well as costs. The Wallbox concept has advantages on every aspect. First, changes in design and construction of the bottom and the top is easy and very flexible, because they consist of two parts. This gives more freedom to construction and design, making the result more attractive and appealing to the consumer. Additionally less plastic material is needed to construct the box, because the bottom, top and body can be thinner, leading to weight and cost savings on material. Discussions are still going on between environmental experts, whether a carton or plastics body of the box would be better to recycle the box after use.
The Wallbox concept supports both possible options for the body. The box can be produced easily with extra coatings like EVOH to preserve the contents longer. In fact the box made for LU allows the food contents to be preserved 3 times longer than before. Finally the box is assembled by the customer, saving space when shipping the box in parts to the filling line. One truck can hold up to 200,000 boxes, significantly reducing the costs of transportation.