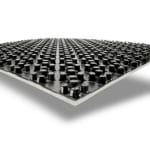
The polymer foam-producing industry currently consumes around 25 million metric tonnes of plastics every year, and is expected to grow by close to 2.5% per year over the next ten years, mainly in building & construction, packaging, transportation, and also furniture.
In the building & construction segment, there is a clear need for low-cost, energy-efficient houses that can be built quickly. In packaging, companies must create new designs that minimize the amount of material needed to ensure that packed contents arrive at consumers in the best possible condition. In automotive, consumers want more comfort and less fuel consumption. Polymer foams provide answers for all these needs, and more.
SABIC has identified "foaming and lightweighting" as an important focus area, where its numerous polymer-based solutions can help the entire value chain become more efficient, more sustainable and more profitable. The company already has more than 35 years of experience in foams and a significant share of the market for foamable polyolefins, with foam grades made in Europe and in Saudi Arabia. SABIC also supplies polystyrene foam solutions into the Middle East and Africa (MEA) market from its operations in Saudi Arabia.
Now, SABIC is expanding its portfolio to include more polyolefins (including POP elastomers and POP plastomers), and engineering thermoplastics such as LEXAN polycarbonate, modified PPE (NORYL) and PEI (ULTEM).
Several breakthrough innovations are in the process of being commercialized. SABIC LDPE 2502X0, for example, offers special benefits for the physical foam extrusion process, as well for the resulting lightweight foams. SABIC LDPE 2402CX0 offers benefits for crosslinkable (XL) foam extrusion processes. The XL foams have an improved properties-to-weight ratio, offering the possibility to use them in higher added-value applications.
SABIC has also developed a new series of "fast converting" foam material solutions that provides further improvements in the production efficiencies of foam manufacturers. SABIC LDPE 2102FC is the first in a series of products that combine up to 50% savings in degassing time - reducing the foam manufacturer's inventory - and an improvement in production efficiency of up to 5% through less production waste and better foam consistency.
Further innovations in polymer foams are already being planned and executed at SABIC's new Foam Innovation Center in the Netherlands. This Center is equipped with most foam process capabilities as well as analytical equipment, enabling SABIC to carry out developments on new foam solutions, technology innovations and collaborative projects with customers, to reduce the material footprint, enable energy and cost reductions, and decrease time to market.
In its Home of Innovation in Saudi Arabia, SABIC is already showcasing the latest solutions for its polymer and foam materials. It continues to push the boundaries of technology to discover even better, more sustainable energy-saving applications.