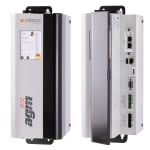
Why does reliable ultrasonic welding play an important part in health protection? The answer is provided by the new AGM Pro ultrasonic generator from Rinco Ultrasonics, which is currently being used to make masks. The generator ensures high production efficiency and high-quality products. It was designed for cutting and welding thermoplastic materials in automation lines or special machines, and boasts exceptional flexibility.
- Simple integration into existing systems thanks to variable fieldbus interfaces
- Intuitive operation via touch display or web app
- Suitable for all automated cutting and welding processes
- Used in automotive, food and textile industries as well as packaging and medical technology
- Reproducibility, traceability and data security included
At the moment, face masks are being produced in greater quantities around the world than virtually any other product. Producing these simple items of PPE involves various steps: first the fabric or non-woven material must be cut to size and welded securely, then the elastic straps are welded into place. Automated mask production using the new AGM Pro ultrasonic generator from ultrasonics specialist Rinco Ultrasonics makes it easier for companies to supply the market with safe products quickly and efficiently.
The new digital ultrasonic generator boasts a number of special features that users can benefit from in this application. The AGM Pro is fully compatible with Industry 4.0. It can be integrated into any system in any environment using interchangeable modules and can then communicate securely via the standard fieldbus interfaces: Profinet, Profibus, DeviceNet, EtherNet/IP, EtherCAT and CANopen. An RS485 interface is also available, along with digital and analogue inputs and outputs.
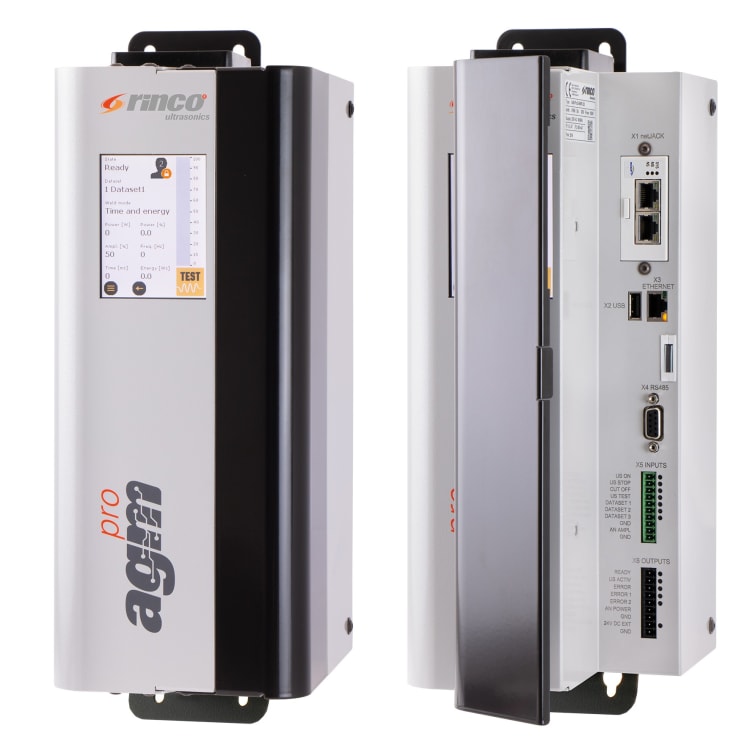
AGM Pro ultrasonic generator with interchangeable fieldbus interfaces
The generator can be operated quickly, flexibly and intuitively via the 3.5-inch touch display or the new ProConnect web application – an invaluable benefit in times where work frequently has to be carried out remotely. This allows parameters to be modified, data to be exported or status messages to be monitored in real time from a distance. Multi-level user administration ensures optimised quality assurance, and maintenance can even be carried out remotely thanks to ProConnect. At the same time, however, the system's own on-site PLC can also be used to operate the new, compact AGM Pro ultrasonic generator at any time.
Eight parameter data sets can be saved in the database, and the user can choose between six welding modes. Welding data can be recorded on a continual basis via a USB port. The data can be traced as each data set has a timestamp.
The AGM Pro packs all of these features into a compact housing. The new ultrasonic generator has a significantly smaller design than its predecessor and weighs half as much. It fits easily in the electrical cabinet and offers two installation options, a protected cable guide and optimised cooling management.