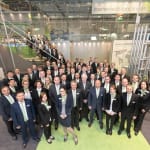
One of the highlights at the booth and a part of the large-diameter pipe extrusion line for the Indian customer was the new solEX NG extruder series. The high-performance extruders of the "next generation" (NG) with their processing length of 40 D have been created on the basis of the proven solEX extruders. However, their completely redesigned process technology concept is setting new benchmarks. A barrel with internal grooves in combination with a matching screw and grooved bushing geometry optimizes the extruder's processing attributes. The result is a lower melt temperature by up to 10°C along with a completely changed axial pressure profile in the feed zone and barrel, which leads to an overall reduction of the load on the system and consequently a cut in energy consumption of up to 15%. "The interest shown by the pipe industry in these new extruders is very lively", Gerold Schley remarks with pleasure and then adds: "Together with our FDC system, which was also on display, the range for pipe manufacturers is very attractive all round."
With its FDC (fast dimension change) system, battenfeld-cincinnati has broken new ground. This pipe dimension change system operates fully automatically across a wide range of diameters and allows not only a change of external diameters, but also of pipe wall thickness during running production. It is perfectly synchronized from pipe head to cutting unit, so that dimension change can be started by the push of a single button. FDC lines cover an enormous bandwidth of diameters, ranging from 90 to 630 mm, which is currently unique on the market. The FDC pipe dies with an adjustable melt gap are available for diameters of up to 1,200 mm, and FDC vacuum tanks, cooling tanks, haul-offs and cutting devices for diameters of up to 1,000 mm.
"At this year's K, the interest in our solutions not only for pipe production but also for the packaging industry was particularly strong", Gerold Schley continues. With its XXL-Multi-Touch roll stack, the machine manufacturer presented an ideal solution for making top-quality, stress-free sheet for packaging at high speeds of more than 110 m/min and with enormous outputs of up to 3,300 kg/h (PET) and 2,700 kg/h (PP). The Multi-Touch roll stacks combined with the proven high-speed extruders are the ideal equipment for high-speed thermoforming sheet extrusion. battenfeld-cincinnati also offers STARextruders, a special machine series for PET processing.
An absolute novelty in the battenfeld-cincinnati product portfolio is a special 3-layer feedblock for thermoforming sheet production, which is completely manufactured in-house in Bad Oeynhausen (Germany). The concept of using a pin with a milled distributor curve to achieve an optimal layer thickness distribution so im-pressed customers that eight orders have already been placed. This is an added incentive for the machine manufacturer to offer this type of technology for 5-, 7- and 9-layer feedblocks in future as well.
battenfeld-cincinnati has seldom had so many new extruders and machine components on show at its booth. Apart from its new solEX NG single screw extruder series, the conEX NG twin screw series for PVC pipe and profile production also celebrated its premiere. These new extruders, too, were created by a complete re-design of the processing unit: a longer pre-heating zone and an optimized screw geometry ensure higher outputs with significantly reduced shear stress and machine wear. All extruders are easy to operate, thanks to the new BCtouch UX control system, featuring clarity and easy handling, which customers could experience first hand directly at the booth.
"The very positive response shows that our motto 'driven by innovation' and constant work on new, innovative solutions has paid off. We will keep this up and will present an even wider range of new technological solutions both in the coming years and at the K 2019", is how Gerold Schley expresses his outlook for the future. At the same time, the machine manufacturer is strengthening its sales and service team to enable it to act even faster and move closer to its customers.