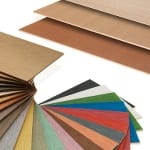
KraussMaffei Berstorff presented its innovative concept for producing weatherproof sheets based on renewable raw materials to a large number of customers during a live demonstration in Munich on March 12, 2014. The customers were able to watch the production of so-called "Resysta" sheets at the TechCenter - which is equipped with a twin-screw extruder in the 32D series. Due to their outstanding property patterns and their deceptively realistic fine wood design, these sheets are primarily used for outdoor applications such as facades.
Successful live demonstration with 60 interested customers
"Our customers showed an unexpectedly high level of interest in this innovative product," emphasized Andreas Kessler, General Sales Manager at KraussMaffei Berstorff in Munich. "We welcomed more than 60 international visitors who provided us with extremely positive feedback on both the production facility and the end product," said Kessler. The sheet production line - equipped with the KMD 90-32/WPC twin-screw extruder and a vertical three-roll polishing stack as the key components - produced 4-mm-thick, 1000-mm-wide Resysta sheets with a guaranteed output of 300 kg/h. During a series of talks focusing primarily on this topic, the customers were also able to obtain more detailed information on the material composition, the production requirements and the end product. Kessler is anticipating a promising future: "Since we are now also seeing greater use of renewable raw materials in sheet extrusion due to growing worldwide demands for sustainable production, we will be able to serve a new market segment with this product in the long term."
Optimum wear resistance of the 32D series for extreme material and process requirements
Processing of natural fiber-reinforced plastics calls for special machine technology, a high degree of process engineering know-how and active wear resistance of the processing unit. "The material mixture supplied by our cooperation partner Resysta is a specially developed fiber-reinforced hybrid material made of ground treated rice husks with an added PVC carrier material," said Peter Oswald, Head of Product Management at KraussMaffei Berstorff. "We systematically geared our machine concept to these requirements: For example, a specific metering device ensures a constant material feed. Since the adapted special venting zone in our 32D twin-screw extruders ensures that the residual moisture can properly escape, the moisture content during the production process remains constantly below 0.6%," added Oswald. A high installed screw torque, coupled with internal screw heat balancing and screw geometry specially modified for the Resysta compound, guarantees a homogeneous melt, thus leading to a premium quality end product. "Another 'must' for Resysta processing machines is active wear resistance," said Oswald. "Screws must have wear proof protection well beyond the normal level of wear resistance while the barrels must also be lined to a correspondingly high degree. This combination ensures maximum protection of the processing unit against corrosive and adhesive wear during processing of the Resysta compound."