Automatic monitoring and smart control of the stretch-blow-molding process
In order to help beverage producers overcome all of these challenges and to provide options beyond manual operator intervention, Krones has developed Contiloop AI.The system, which is fully integrated into the stretch blow molder, measures the light transmission ratio at as many as 32 points on each container. During ongoing production, Contiloop AI responds to even the slightest variations in material distribution and automatically adjusts the stretch blow molding process in real time. It also takes into account additional parameters such as ambient temperature and humidity as well as preform feed and discharge temperatures. Any adjustments made are displayed on the HMI to give the operator a clear overview of the current process controls.
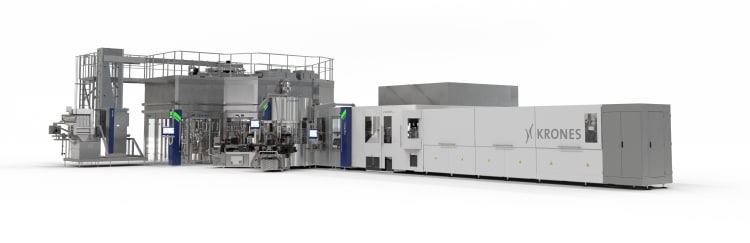
Artificial intelligence makes it possible to train and optimize the system
Because production conditions are constantly changing, it’s not enough for Krones to have the controls revert to a specific, pre-set formula. Instead, various initial process settings are made for the system in an automated trial run and the resulting measurements are passed on to the Krones IIoT (Industrial Internet of Things) platform. There, the data flows into the Krones AI pipeline and is used to train the rule algorithm, the “intelligent agent”. When training is complete, the agent is loaded onto the machine’s Contiloop AI and is then available for use in production operations.“The advantages of this system are clear: On the one hand, Krones can make available AI agents that are suited to additional container types that might in future be processed on the same machine - in a way that is secure and convenient for the customer. On the other hand, existing agents are regularly checked and can be retrained as needed at any time, for instance, if there are significant changes to production conditions - so they can become even smarter,” explains Robert Aust, Head of Product Management Plastics and Bloc Technology at Krones.
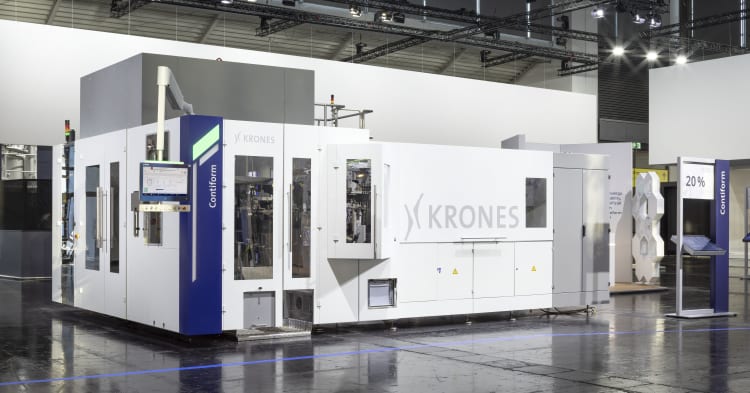
Especially worthwhile when processing rPET
But the myriad advantages of Contiloop AI are not limited to material and process aspects – this ingenious technology also makes work considerably easier for operating personnel. The automated controls mean far fewer manual interventions at the machine, and offline quality assurance can be reduced to a minimum.
Looking ahead to the future
At Krones, we’ve long placed a strong emphasis on combining ease of operation with the highest level of quality. And so, Krones will continue to develop Contiloop AI and use cloud- and AI-based technologies to expand the system’s capabilities - to even better help our customers master the challenges of day-to-day production.