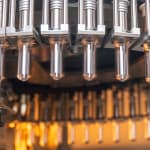
With Contiloop AI, Krones has developed an intelligent process control system for the Contiform stretch blow molder: The combination of AI-based software and newly developed hardware makes it possible to detect even the slightest variations in material distribution in the production of PET containers and to automatically adjust key stretch-blow-molding parameters in real time - and thus to ensure that bottle quality meets specifications.
The challenges associated with manufacturing PET containers are varied and complex. Process windows are short, and even the daily changes in ambient temperature and humidity in the production hall require regular manual adjustments to various process parameters to ensure the required level of container quality.
Steadily increasing production speeds present another challenge: While the maximum output per blowing station was still at 1,600 containers per hour back in 2000, today’s stations are capable of making up to 2,750 bottles per hour. So, a machine can turn out as many as 100,000 containers per hour. Of course, at such high speeds, even the slightest deviations from ideal conditions can quickly and significantly impact an entire production run.
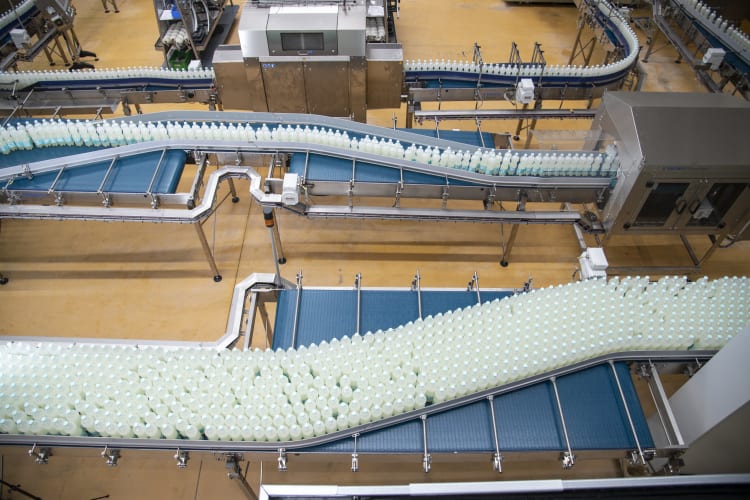
Temperature variations in the production hall throughout the day often necessitate adjustments to process parameters on the stretch blow molder. Contiloop AI now takes care of those adjustments, fully automatically.
Meanwhile, demands on personnel are also evolving: State-of-the-art technologies and increasing automation in all areas of filling mean that it takes fewer people to run the machines and ensure successful production. Today, one operator is responsible for multiple machines and systems - and has less time for visual quality checks and manual process control on the stretch blow molder.
Two more important trends must also be borne in mind: First, consumers especially are calling for increased use of recycled PET material (rPET). In order to combine the advantages of PET containers with sustainability, beverage producers must gradually increase the share of rPET in bottles to as much as 100 percent. But not all rPET is created equal. Quality and composition are critical factors - and they can sometimes be rather uneven. Any inconsistencies must be offset in the blow molding process, to ensure that every container meets the specified quality criteria.
The second trend is the continued effort among beverage producers to further reduce the weight of their bottles. PET (whether recycled or virgin material) is costly, and high-quality rPET is a scarce commodity. And so it only makes sense to reduce the weight of the containers as much as possible - to save on materials in the production process and to further reduce the containers’ ecological footprint.
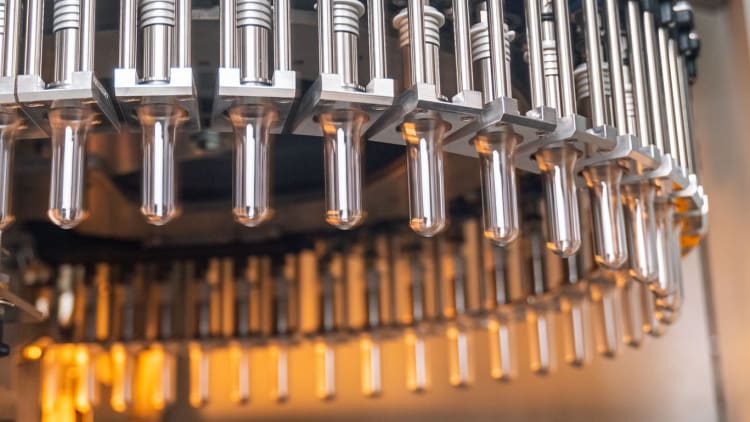
Not all rPET is the same, it depends on the quality and composition of the material - and it is precisely these sometimes fluctuating properties that have to be compensated for in the stretch blow molding process, because ultimately every container produced should meet the set quality requirements. Contiloop AI makes exactly this possible.