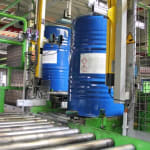
Throughout the facility, no buffer stock is kept at individual processing stations. In the event of the transportation system stopping due to a jammed barrel or malfunction, the output of the production process can be impacted.
BASF realised that the control systems of 25-year old transportation system was outdated, and needed to be revised to meet modern manufacturing requirements.
The original plant control system
The system was controlled by three old PLCs (programmable logic controllers) that could not be supported, as spare parts were no-longer manufactured. The safety levels were not state-of-the-art and BASF had no plant visualisation. No manual correction action could be taken prior to a failure.The decision was taken to improve both the automation process and enhance the safety technology. A further stipulation was that the 50 three-phase motors driving the transportation system had to remain operational during the upgrade.
The solution
A central PLC was employed to autonomously control the barrel transportation system. This simplified the automation architecture and the consolidation into one control cabinet freed up valuable space on the production floor. At critical points in the system, operator panels were installed to aid visualisation. Operators could identify barrels that were not been removed from the transport mechanism in real-time, and easily see where congestion was occurring.The panels are also able to provide information for preventative maintenance as the system displays the type of error occurring. The ability to distinguish if a run-time error is due to a drive overcurrent event or a frequent start-stop condition for example, provides valuable information to the maintenance teams. Proactive action can now be taken to test the drives or preform an inspection of the mechanical system.
To enable error detection, the BASF team paid close attention to measuring the current drawn by the drive motors. “This was the main reason for us to wire the control cabinet with Eaton’s SmartWire-DT intelligent wiring system,” explains Thomas Büch, a member of Site Engineering Lemförde’s Technical Team.
The switchgear and drives are not connected with individual point-to-point wiring with the control panel; instead SmartWire-DT uses an eight-pole flat cable. The one cable supplies all the devices with power and simultaneously takes care of the data communication.
“By using system tools and components, wiring errors are virtually eliminated,” explains Thomas Gern, Head of the Industrial Systems Technology department at Elektro-Anlagen-Technik EAT GmbH. Based in Wallenhorst, Germany, the electro-technical service provider built the control cabinets for the BASF plant. “Routine testing of the cabinet can therefore take place within a very short time. After a brief system introduction at our end, our control cabinet makers were able to complete wiring in half the time in comparison with conventional point-to-point wiring.”
With the use of various operator panels spread across the system, to which the SmartWire-DT system communicates the information, the employees can see when and why a fault or downtime occurs.