“Adapted Machine” for elastomer processing from Maplan’s “Modular Kit”
The high standard which is set to the mould is reflected also in the machine technology. The horizontal injection moulding machine MHF700/300XLeditionS from Maplan is equipped with some special options from the manufacturers modular kit fitting to the injection process. Besides higher reproducibility and injection capacity, the FIFO dual injection unit is equipped with a nozzle retract and is now also available in “1200-ccm execution“. The energy concept of the drive corresponds to the Cool Drive II Standard. A very short nozzle assures maximal injection pressure directly on the cold runner. The operator can control all process parameters of the machine transparently via a proven user interface of the 5th generation of control. Highest precision and the FIFO System are coupled with energy efficiency and low cost of maintenance as well as quick material and colour change if required. The daylight of the machine has been increased to 850 mm while the minimum mould height of 40 mm remains unchanged. Thus the machine covers all current mould concepts from simple two-plate moulds to cold-runner systems with automatic demoulding. The brushing system is made by Rubber System and consists of an electrically driven single-arm servo brush with horizontal adjustment for effective demoulding of parts.
To the point: Configuration of the component of quality assurance system
The task of GiBiTre instruments is to plan the entire production process and to create production related work equipments for measurements and tests. GiBiTre has at its disposal a consolidated horizon of experience in processing elastomers. This includes effective tests of not vulcanised compounds as well as the test of the finished rubber moulded parts.
It’s come full circle: Integrated reworking and zero-defect manufacturing
From Gamma Stampi comes the punching machine for separating parts. It guarantees a perfect job punching out the sealings and hence avoid “reworking”. This not only saves time and costs, but also makes the parts directly available for final inspection. The final inspection is carried out by devices from UTP Vison which is a manufacturer of high precision equipments for “intelligent inspection”. Their tasks are twofold: testing quality of parts and sorting out faulty parts. The inspection consists of an optical test installation. It checks the dimensional accuracy of the sealings, surface finish and injection deviation. Sealings that do not meet the required criteria are sorted out via a turnout. The finished parts can then be shipped directly to the processors. The inspection module of UTP Vision is thus an important tool for zero-defect manufacturing in elastomer processing.
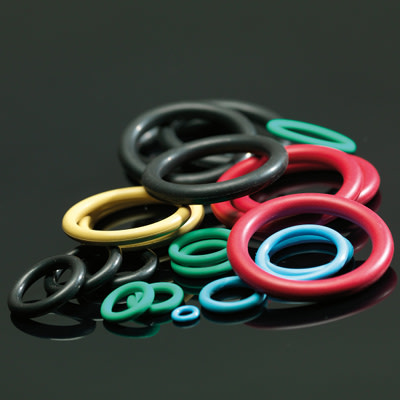