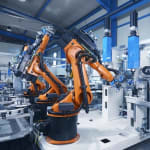
Especially in sectors where technology is such a strong driving force - such as the automotive industry - the vision of Industry 4.0 is becoming more relevant as time goes on, thanks to increased digitization and the growth of machine and system networking. Even so, not all market players are equally aware of the diverse possibilities for networking that are now available in automated production; nor do they fully appreciate the economic benefits that more transparent production processes can also deliver. As a leading provider of process monitoring systems, Kistler has set itself a specific goal at this year's Motek: to focus attention on this highly relevant issue by showcasing prominent examples of the technologies involved. For joining, forming and testing processes alike: Kistler offers complete systems - from the sensor to the evaluation unit - that can map processes accurately, enabling comparisons and evaluations on a standardized basis across the globe thanks to a consistent operating philosophy.
Electromechanical Joining Systems: Another Addition to Kistler's Portfolio
At this year's Motek, Kistler will premiere its new NCFE (Economy) electromechanical joining module. This new product has been specifically developed for plant manufacturers and operators of conventional power packs. The functionality and design of the NCFE are deliberately geared to simple joining tasks. Plant manufacturers and operators of power packs who opt for the NCFE will benefit from a pre-tested system with integrated process control. This saves time and money on the development of users' own systems - and, because all Kistler process monitoring systems are based on a uniform operating philosophy, seamless integration into the overarching production environment is guaranteed. The NCFE is available for applications in the 10-80 kN measuring range. Kistler is also presenting its NCFR joining module - as well as the classical linear joining process, this system can perform a controlled rotary movement of the ram, either sequentially or even simultaneously.Like the entire family of NC joining systems, all three new products deliver a host of benefits for their users: they offer great flexibility and excellent dynamics combined with simple operation - so simple as well as highly complex joining processes can be implemented rapidly and efficiently with one and the same product family. Thanks to the servo amplifiers used in the products, all traverse movements that are performed can be controlled with high precision. Another example: users of NCFH joining systems can switch between measuring ranges, so completely different components can be manufactured on one and the same plant. Furthermore, end-to-end standardization of the systems means that users can easily obtain spare parts - anywhere in the world. But at the end of the day, future users will probably be convinced by one argument above all others: thanks to their excellent flexibility and low energy consumption, all the joining systems can help the automobile industry and the automotive supply sector to achieve lasting reductions in their series production costs.
maXYmos TL 1.2 and maXYmos BL 2.3: the Latest Generation of Monitoring Systems
Yet another highlight is in store for visitors to Kistler's stand: the latest generation of maXYmos monitoring systems. Their purpose: to deliver consistent process-integrated quality assurance. The patterns of measurement curves can be used to monitor and control the quality of a single production step, a sub-assembly or an entire product. Now, maXYmos users can also measure multi-stage production processes (i.e. those with consecutive staggered steps): this has been made possible by equipping the maXYmos TL 1.2 and BL 2.3 with a sequencer mode, in the same way as the successful maXYmos NC. The benefits for users are clear to see: thanks to integrated process control, test processes can now be mapped with no need for costly external PLC programming. The programs can be set up quickly and easily with the help of the intuitive user interface on the touch display. Even for multi-stage processes, optimal cycle times can be achieved with maximum repeat accuracy. Because this control is integrated in the process, the system provides the basis for enhanced transparency in assembly and testing lines - paving the way for increased cost-efficiency throughout the production facility.4503B Torque Sensor: the Rugged Sensor for Maximum Accuracy
Kistler's stand at the Motek will also present the latest state-of-the-art in high-precision torque sensor technology: the Type 4503B torque sensor, which offers a wide range of additional functions. On this new sensor, for instance, optical speed and angle sensing has now been replaced by magnetic technology. This gives the sensor added resilience for reliable operation in heavily contaminated industrial environments - thereby saving valuable time on maintenance. The torque sensor's electronics have also been optimized, and the 4503B now has a cut-off frequency of 10 kHz for highly dynamic measurements. Users can adjust this value individually with the help of an integrated digital low-pass filter, and the second measuring range is freely scalable up to a spread of 1:10. Outstanding features of the Type 4503B also include wide measuring ranges (from 0.2 to 5,000 Nm), integrated speed/angle sensing of up to 8192 pulses/revolution and a high-speedversion with up to 50,000 revolutions per minute (1 min/rpm).
If you want to see Kistler's diverse range of solutions for interconnected quality monitoring at first hand, save the dates for the trade show now: it runs from 10 to 13 October 2016 at Motek in Stuttgart.