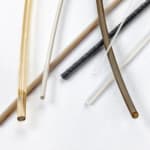
IPE has seen growing customer demand for extrusions made of high-performance thermoplastics due to their ease of manufacturing and strong property profile. In particular, the company has seen a major shift toward replacing metals and thermoset materials with advanced thermoplastics in medical applications, according to Jonathan Jurgaitis, melt extrusion manager for IPE.
"Based on the demand from our customers, it's clear that these high-performance materials have a strong track record, and the industry is familiar with them as a viable option for a range of applications," Jurgaitis said. "IPE has worked closely with Solvay by tapping into their technical expertise to develop custom products that meet the stringent requirements of demanding end-use applications in the medical, aerospace, and military industries."
IPE chose Solvay's sulfone polymers due to their excellent clarity, stiffness and steam sterilizability. Specifically, IPE used Solvay's Udel polysulfone (PSU) resin to fabricate 0.02-in (0.5-mm) monofilaments and Radel polyphenylsulfone (PPSU) resin to make 0.06-in (1.5 mm) and 0.11-in (2.8 mm) monofilaments. It also used Radel PPSU resin to make 0.50-in (12.7 mm) microbore tubing with outer diameter (OD) of 0.012-in and inner diameter (ID) of 0.010-in (0.3 mm OD x 0.25 mm ID).