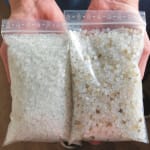
Around 12,000 tonnes per year of sorted granulates leave the new granulate sorting centre of Sortco GmbH & Co. KG in Niederzissen. "With innovative mechanical and optoelectronic sorting systems, we guarantee the highest granulate purities and our special know-how enables us to meet the highest quality requirements of our clients" introduces managing director Lars Ruttmann the service of his company, which has its headquarters in Hamburg. "The goal is the safe and reliable sorting out of unavoidable impurities that could lead to machine downtime, expensive repairs of tools and hot runner systems and cause complaints and image damage during subsequent processing."
Stips, burns, greying, and black specks cannot be avoided in the production of compounds and pellets. Even though the number of defects is usually low, these small defects can have a major negative impact on the production of particularly cost-intensive or sensitive components. Rejects are the result, which is annoying and expensive, and highly unecological, just like an unnecessary waste of energy and personnel costs.
Sortco GmbH & Co. KG offers its sorting service to prevent such problems. The order can vary from 1 tonne to several 100 tonnes. "We can sort average goods with high contamination rates as well as reliably detect and discharge small amounts of contamination in granulate batches," Lars Ruttmann points to a wide range of applications.
After all, he relies on state-of-the-art detection and sorting technology at his new company location in Niederzissen. In addition to mechanical separation systems such as dust collectors and metal separators, various optoelectronic sorting systems ensure the best results. Colour deviations from a of 50 x 50 µm can be detected and removed in any free-flowing granulate. The result is a virtually defect-free granulate that the customer can choose to receive back in sacks, octabins, or big bags and use in any application without any problems.
Many customers, mostly international plastics producers and compounders have long since placed their trust in Sortco's expertise and can thus in turn provide their customers, the plastics processors, with the highest degree of safety for component production. A classic win-win situation that is both economical and resource-saving.
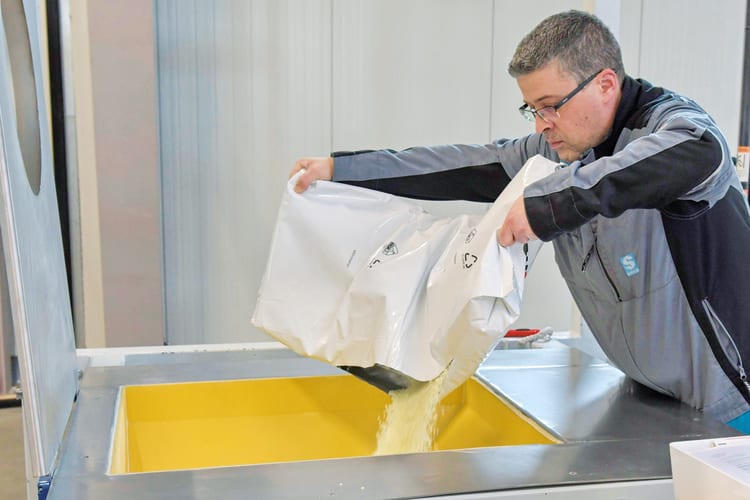