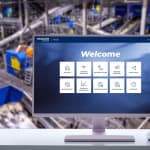
Stadler Anlagenbau GmbH, the globally active German company specialised in the planning, production and assembly of turnkey recycling and sorting plants, is transforming plant operations with its digital solutions developed specifically for sorting facilities. Its cloud-based platform Stadlerconnect provides a single access point for the company’s digital solutions and harnesses machine and material data to optimise sorting plant performance. By pioneering digital solutions, Stadler is advancing the recycling industry towards a new era of smart, data-driven sorting plants.
Stadler is transforming recycling plant efficiency with its digital solutions specifically tailored for sorting plants with a focus on optimising operations. Through its comprehensive cloud-based platform Stadlerconnect, the company offers recycling and sorting plants a single-access-point solution for its digital products, helping them unlock the full potential of machine and material data to drive impactful operational improvements. It is designed to deliver added value to recycling plants of all types and s and offers customized views for both operators and management.
With digital solutions taking on an increasingly critical role in the recycling industry, Stadler has made it a core strategic priority - both in its operations and in the sorting plants it designs. Julia Stadler, Chief Digital Officer, explains: “At Stadler, we view digital solutions as crucial for maximizing the performance of recycling plants, positioning them as a core part of our innovation leadership. Our strategy centres on sustaining our role as the market leader and a pioneer in designing and building turnkey recycling facilities.”
Avoiding Downtime with Predictive Maintenance
Predictive Maintenance, one of the Stadlerconnect modules, enables a proactive approach to equipment maintenance with the help of sensors, providing operators with instant alerts on any critical changes in sensor data before potential issues arise. This early warning capability allows for immediate inspections, minimising costly production delays and reducing the risk of sudden breakdowns.
Andreas Stöcker, Deputy Operations Manager at Reiling has seen notable benefits with this system: “The installation of Predictive Maintenance resulted in easier maintenance and allowed for forward-thinking planning of service work, as every small change to the machine is immediately reported. Before we decided on this solution, some bearing damage would occur very suddenly. With the measuring system, we can prevent this issue from happening. From the short time we have been using the measuring system, I can say that it should be installed on every machine from the beginning, although, including it subsequently makes sense as well.”
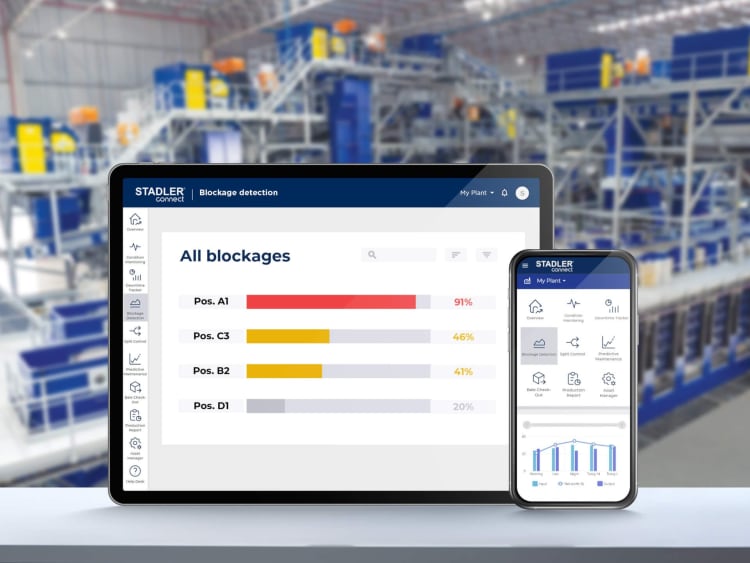
“From a planning perspective, we’ve seen significant improvement,” said Pieter Van Camp, Lead of Maintenance at Indaver another customer using Stadlerconnect at its sorting plant. “Operating at a high level of technical availability (95%), every instance of downtime greatly impacts production. With the implementation of these sensors, we feel more secure knowing we can continuously monitor the condition of our machinery. For example, by monitoring the ballistic shafts, we can track their condition in real time and observe any decline in performance. This capability allows us to extend their operational lifespan and precisely determine the optimal time for replacement. As a result, we’re saving both time and money! Overall, our experience with the wireless sensor system has been transformative.”
Stadler’s Digital Solutions: Driving Efficiency and Customer Value in Sorting Plants
In developing its digital solutions, Stadler has pursued a twofold objective: delivering added value by using key data insights to enhance plant operations, and applying these insights to improve both plant design and after-sales service.
“Our digital solutions are purpose-built for sorting plants, directly addressing the needs of plant operators,” says Julia Stadler. “Leveraging our extensive OEM expertise, we ensure greater accuracy in areas such as determining conveyor equipment status. Our team combines software development and engineering expertise. This approach goes beyond simple data collection and visualisation: our solutions leverage new and existing data points to drive meaningful operational improvements.”