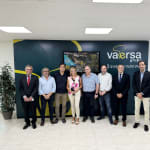
Stadler Anlagenbau GmbH, the globally active German company specialising in the planning, production and assembly of turnkey recycling and sorting plants, has designed and built a state-of-the-art light packaging sorting plant for public enterprise Vaersa in Alzira, Spain.
The opening ceremony of the new Vaersa light packaging plant designed and built by Stadler in Alzira - a benchmark in the Spanish waste management sector - took place on the 3rd of July, in the presence of the leading local government representatives with environmental responsibilities Salomé Pradas, Councillor of Environment, Water, Infrastructure and Territory, Francisco Javier Sendra, Regional Secretary of Environment and Territory and Jorge Blanco, Director General of Quality and Environmental Education. Also in attendance were representatives of top management from Vaersa José Alberto Comos, General Manager and Raúl Esteban, Deputy Manager, as well as Ismael Avilés Ortega, Operations Manager Spain at Stadler, Vicent Estruch, President of the V4 Ribera-Valdigna Consortium and Alfons Dominguez, Mayor of Alzira.
Noelia Almiñana Lledó, Head of Vaersa's Waste Department, opened the proceedings by recalling the beginnings of the Alzira site with a manual sorting plant back in 2000. She highlighted the progress achieved through Stadler’s automation of the process and emphad that the plant will ensure the correct recovery of light packaging from now on. José David Castillo Cáceres, Alzira Light Packaging Sorting Plant Manager, took over with a presentation of the new plant. A video of the construction project and the sorting line in operation closed the event.
Vaersa’s requirements: more capacity and quality through automation
Vaersa is a public enterprise reporting to the Department of Agriculture, Rural Development, Ecological Transition, and Climate Emergency of the Generalitat Valenciana (government of the Valencian Autonomous Community). It provides services related to environmental management, including waste management aimed at achieving a circular economy. It began managing the light packaging sorting infrastructure for the Valencian Community in 2000, coinciding with the implementation of separate waste collection. The facilities include the light packaging plant in Alzira, the oldest of the four it operates.
In 2023, Vaersa decided to invest in upgrading and expanding the capacity of the Alzira plant to address the increasing volumes of light packaging waste and to improve the quality of the output for recycling. As a public enterprise, it issued a call for tenders to award the project under the Public Sector Contracts Law. The tender criteria included designing the sorting line to prioritise maximising recovery, facilitate operation and ease of movement within the facility, and enhance operating efficiency through the placement of every piece of equipment and their implementation. Ergonomics and safety of plant personnel in all aspects of operation, from sorting tasks and quality control to cleaning, operation and maintenance were key for the project. The tender criteria also required to include an analysis of preventive and corrective maintenance, and measures to ensure the processing line’s modularity and flexibility.
Stadler presented a highly detailed preliminary project, which was the highest rated by the contracting committee, and was awarded the contract. Noelia Almiñana Lledó explains: “The Alzira Packaging Sorting Plant was the oldest of the Vaersa Plants and therefore the least automated. Our foremost and greatest challenge was to implement an automated processing line that would double the existing plant’s capacity in the same space. Stadler designed a compact process line that fits the available space, incorporating the most modern sorting technology without compromising its operation, performance and efficiency.”
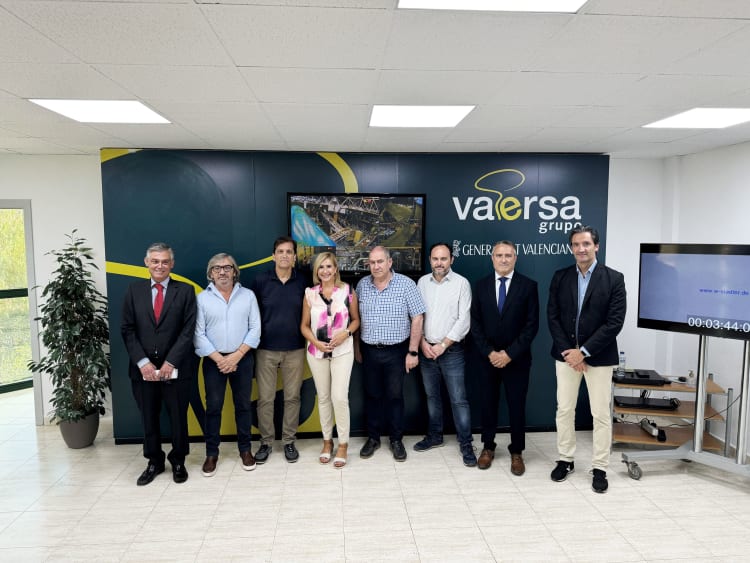
Stadler’s solution: more than double the capacity, higher output quality, future-proof
The new plant increases the facility’s capacity from 3 t/h to 8 t/h, making it one of the largest sorting plants in Spain by capacity. Installation in the same building as its predecessor introduced significant space constraints, which Stadler’s design successfully addressed: “One of the main challenges was that we were replacing an existing plant,” explains Ismael Avilés Ortega, Operations Manager Spain at Stadler. “This required a meticulously studied design to fit within the existing building, making the preparatory work of our engineers crucial.”
Stadler’s design for the new plant automates the sorting process with two sorting cabins, two Stadler STT2000 ballistic separators that separate the flexible and 3D materials, magnetic and eddy current separators that sort metals into ferrous and non-ferrous, and optical sorters that recover recycling materials. The output is sorted into PET, HDPE, film, Tetra-Pak, plastic mix, and ferrous and non-ferrous metals. At the end of the process, the recovered materials are baled and sent for recycling. The new plant design also enhances the efficiency of the sorting process and improves the quality of the output fractions, supporting Vaersa’s commitment to advancing towards a circular economy.
Stadler’s design stands out for the flexibility and modularity of the processing line. This means that Vaersa can rely on uninterrupted operation: “Bypass systems have been designed to ensure continuous treatment in the event of critical equipment shutdowns,” comments Jose David Castillo Cáceres. “We also appreciate the standardization of mechanical and electrical equipment and components which helps optimize the management of spare parts.”
Stadler’s solution future-proofs the Alzira sorting plant. Its flexibility allows for further expansion in the plant’s capacity to absorb the expected increase in incoming waste resulting from growing public awareness and commitment to separation at source. In addition, it addresses possible changes in the incoming waste due to “its ability to adapt to potential changes in the characteristics and composition of the input materials. To this end, Stadler has allocated space reserves that will allow for the future installation of new equipment for possible process adaptations,” explains Jose David Castillo Cáceres.
A successful collaboration
Effective communication and close collaboration of all parties involved in the development and implementation were critical to a successful outcome due to the complexity of the project. “It involved dismantling the complete existing plant, which was done in record time. Other companies performed civil works, so good communication and coordination were essential,” says Ismael Avilés Ortega.
“It’s worth highlighting the good planning of the works and compliance with all the execution deadlines. We are impressed by the professionalism of Stadler’s highly qualified staff, the technical capability of its entire team, from the Projects Department, which designs the best possible solution for the requirements, to the assembly staff, always available to resolve any unforeseen event,” adds Noelia Almiñana Lledó. “Indeed, during the project’s development, improvements to the original design were implemented and Stadler consistently addressed them promptly and effectively, without impacting the scheduled completion timeline,” concludes Diana Torres, Project Manager at Vaersa.