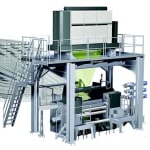
Mobile, flexible production assistants are coming to factories, bringing fast reaction times - exactly what’s required for rapid, individualized manufacturing. Stäubli, one of the world’s leading providers of mechatronic solutions, is showcasing its groundbreaking technologies at the 2019 Hannover Messe and demonstrating how flexible production systems can already be reality.
Where human beings reach their limits is where Stäubli’s mobile production solutions and interfaces help overcome them. Mobile, flexible production systems facilitate extremely versatile production on an industrial scale. They save time and money, and enable production individualisation. It can take weeks to switch a production line over to a new product. However, mobile, modular manufacturing makes it possible to reconfigure production jobs in a matter of minutes - based on current workload or customer wishes. The result is a complex interaction of many components that calls for technical expertise and innovative thinking.
Robotic co-workers handle the nightshift
Stäubli’s HelMo robot system loosens the rigid corset of automation and achieves an utterly unparalleled level of flexibility thanks to its mobility. HelMo can travel fully autonomously and navigate itself within its production environment. Mobile operation and autonomy are facilitated by generously proportioned energy storage. At the heart of the system is a powerful standard robot with minimal modifications – in this case, a robot from the reliable TX2 range. Stäubli recently augmented its expertise in the field of mobile production systems through its acquisition of a majority shareholding in mobile transportation specialists WFT from Sulzbach-Rosenberg in Bavaria, Germany.
“The combination of robot technology and a mobile transport platform has enabled us to create a flexible production system able to handle complex tasks previously considered unfeasible for automation,” says Peter Pühringer, Division Manager Stäubli Robotics. These include, for instance, loading and unloading as well as the linking of machine tools. In future, users will be able to produce in Industry 4.0 environments and count on a significant gain in autonomy, flexibility and productivity. “It also means HelMo is able to work longer hours than its human colleagues and handle the nightshift, too,” says Pühringer, continuing: “It all adds up to an extremely popular team member.”
The right interface is crucial
This step towards flexible production processes is also aided by the new developments generated by Stäubli Electrical Connectors. “Driverless Transport Systems” (DTS), the electric vehicles used in HelMo or in logistics applications, are a fixed feature of forward-looking production and supply-chain processes,” says Thomas Spindler, Head of Sales & Marketing for Stäubli Electrical Connectors in Germany. “To ensure precise, powerful, safe and time-saving charging of the energy storage units, we developed the automatic QCC (Quick Charging Connection), as used in facilities such as container ports.”
Furthermore, fully configurable connectors with the modular CombiTac system ensure that mobile production units can access all their requirements for power, signal and data transfer with just one single connector. It can even accommodate hydraulic and fluid couplings. The HelMo system also uses this technology to supply the mobile robots with the resources they need at their workstation.
Tool-changing systems enhance production systems
Stäubli also forms reliable connections through the technologies from its Fluid Connectors division. Taking centre stage at the Hannover Messe are tool-changing systems for robots that now cover all loads. The compact, lightweight tool-changer variants, in particular, help mobile production systems like HelMo cover an extremely wide range of tasks. “We’ve been working for years with WFT, which specialises in mobile production systems. In order to meet the sector’s standards, our connector solutions feature compact configurations that guarantee reliable functionality and exceptional safety standards,” says Norbert Ermer, General Manager Stäubli Fluid Connectors in Bayreuth. “Our smaller models are particularly beneficial, as their weight-optimised configuration means users don’t have to invest in robots from the next-higher load class.” To guarantee maximum functional reliability, Stäubli is the only manufacturer worldwide to develop and produce the changers entirely in-house.