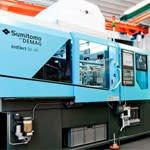
The German/Japanese mechanical engineering company will demonstrate the efficiency, precision and reproducibility of its IntElect machine to international specialists from the medical sector. This machine will show its high reliability and availability in the production of precision components for medical, diagnostic and pharmaceutical applications under cleanroom conditions.
At the MEDTEC Europe 2011 trade fair the smallest model of the IntElect series, an IntElect 50-45 with a clamping force of 500 kN, will be seen producing control knobs with a diameter of 3.5 mm made of polyacetal (POM) for hearing aid devices in a cycle time of 10 seconds. These mouldings, weighing a mere 10 milligrams and having a shot weight of only 280 milligrams, make high demands on quality, and require absolute reproducibility. The IntElect machines, with their precise and sensitive drives and automation integrated in the machine, satisfy these specific requirements with zero-defect production.
Sumitomo (SHI) Demag have designed and developed this production cell in a joint effort with several partners. The four-cavity cold runner mould with a tunnel gate was designed and built by Stamm AG of Hallau/Switzerland. This established mould making and injection moulding contractor specializes in the production of particularly challenging micro mouldings from a wide variety of different plastic materials and uses a number of machines supplied by Sumitomo (SHI) Demag.
The cell, built according to cleanroom standards, and the laminar flow unit above the production system have been made by Max Petek Reinraumtechnik of Radolfzell / Germany. The filter fan unit (FFU) of the laminar flow unit purifies the air brought in from the outside, and provides a constant laminar air flow above the mould mounting space of the machine, which guarantees a cleanroom class ISO 7 production environment, and prevents particles from entering.
MAi GmbH & Co. KG of Küps, Germany, a specialist in automation solutions, integrated the six-axis robot from Yaskawa Europe GmbH into the injection moulding machine, whose guarding is extended by only 200 mm on the non-operator side. This robot is suspended on the stationary platen. This design and configuration keeps the cell compact, the mass to be moved low and the robot's strokes short. It also ensures that the susceptible mouldings are
far less likely to become contaminated during unloading, inspection and packaging. The control knobs are even subjected to a complete, fully automatic visual inspection within the cleanroom production cell.
With the IntElect smart, its NC5 control system and its broad catalogue of options, Sumitomo (SHI) Demag offers injection moulders a flexible and economical machine, selected from the modular system of its electric machine range. Owing to its many features, the IntElect 50 is well equipped to produce medical plastic components, even in its basic configuration. It features large tie bar clearances, linear guidance for maximum platen parallelism, outstanding reproducibility and process capabilities as well as high levels of reliability and availability.