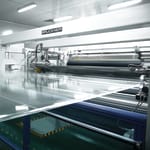
Brückner Maschinenbau is working on a means to make films with the highest possible recycling capabilities producible on film stretching lines. The focus is on mono-material film with superior mechanical and optical properties, which will be able to substitute previous multi-layer films made from different materials. These are ideal for the use in new, single-origin packaging and guarantee good sortibility in waste separation and optimal recycling.
Combination of BOPE and BOPP production
For the K 2019 Brückner will introduce two completely new line concepts for the production of BOPE films (biaxially oriented polyethylene). Film producers can chose between a working width of 6.6 m and an output of 3 t/h, or a working width of 8.7 m and an output of 5 t/h. These are 5 layer concepts for an extended range of films.
The new lines also have the flexibility to produce BOPP films: Specialities such as UHB films and coated films for high-barrier uses alongside conventional packaging film. As the demand for innovative BOPE films is only now starting to develop, film producers will be able to react swiftly and flexibly to market trends.
New inline coater
Even if recycling stands at the forefront of a circular economy, new mono-material structures must fulfil the highest demands and must not be inferior to previous packaging films. This is why Brückner has developed a new inline coater for all BOPP and BOPE lines, installed in the line before the transversal stretching, it makes the production of extremely thin functional layers within the nano-range possible. Due to the extreme thinness, the layers don’t disrupt the sorting and recycling, but cater, for example, for an improved adherence during metallising and excellent barriers in combination with the equally thin but effective aluminium oxide coating.
The focus remains on raw material and energy saving
Despite all developments for the rapidly developing circular economy, Brückner Maschinenbau is keeping to its own ambitious objectives for a decreasing raw material usage and an increasingly minimal energy consumption during film production. Despite all legitimate demands about recycling and reusability, the challenge of climate change and the reduction of the carbon footprint throughout the entire packaging production chain must not be forgotten. In the fight against climate change, we will still need plastic packaging that is produced in a resource-saving way.
Speciality film lines
Alongside stretching lines for the production of packaging films, machines for speciality films are becoming more important in Brückner’s portfolio. The company will be presenting various innovations for the K 2019:
- New high-temperature concept for BOPP capacitor film – this is interesting, for example, for the use in electrical components installed near motors
- Lines for the production of stone paper based on BOPP or BOPE with a calcium carbonate proportion of over 60%: not only with good printability and waterproof, but also environmentally friendly in production
- Biaxially oriented polyester films (BOPET) for optical applications. Brückner’s new, patent pending Relax System ensures homogenous film properties and thus high film quality and better processability
- BOPI (biaxially oriented polyimide) is perfect for flexible optical applications, e.g. flexible displays. The stretching ovens and systems need to be suitable for very high temperatures of up to 400°C, is in Brückner’s new line concepts.
Battery separator films: New technologies for growing markets
In the field of battery separator film for lithium-ion batteries, Brückner Maschinenbau has made a good name for itself in the market with leading film manufacturers thanks to its successfully running lines. At the K they will be presenting:
- Optimised simultaneous LISIM technology
- For less edge trim and thus higher film gain
- For more flexibility in the stretching profile adjustment during operation: improved mechanical properties such as puncture resistance and optimised pore distribution for a longer lifespan
- Newly developed and patented relax chain for improved film properties in regard to battery safety
- 5.5 m line width – globally unique for higher efficiency
- Continued development of its own patented production process, the Evapore process, offering a more environmentally friendly alternative for the production of membrane films
Source: Brückner Maschinenbau GmbH & Co. KG