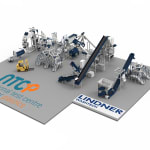
Europe’s first independent testing and research centre with facilities on industrial scale, the NTCP (National Test centre Circular Plastics), in the Netherlands, founded in 2018, has set out to examine the behaviour of different plastics during sorting and washing. The goal is to optimise processes quantitatively, qualitatively and with more efficient energy use, in order to promote plastics recycling in line with the circular economy model. Dutch and foreign clients are already showing great interest in the testing options. "With its modular design, Lindner Washtech’s plastic washing system, to be installed in mid-2022, will make a significant contribution to our research and the optimisation of various plastic streams," says Martine Brandsma, director of the NTCP.
Tucked away in Friesland, a northern Dutch province, lies the 50.000-strong community of Heerenveen. Since 2018, it has also been home to the National Test centre Circular Plastics (NTCP). It is Europe’s first independent testing and research centre which can analyse heterogeneous plastic waste streams down to the smallest part. Rather than relying on usual test set-ups which are commonly used in research institutions, it is instead equipped with state-of-the-art facilities: raw, industrial, noisy and... using real waste.
Playing with the settings
NTCP’s concept is actually quite simple: the more plastic that enters the correct sorting stream and then takes the correct route to the relevant mechanical and chemical recyclers, the higher the percentage of plastics that remain in the loop. Though this may sound simple in theory, the reality is more complex. According to Brandsma, “It’s like a chess game, played on seven boards all at once – and chess moves are being made on each one.” When one applies this to recycling, this means that everyone who takes part in the process – be it the collectors, sorters or recyclers – is in a constant state of development. This means that the system too is constantly changing. In order to examine individual or larger steps in the process, the NTCP has a 25 by 20 metre long, and 9 metre high, industrial sorting system. This simulates the entire sorting process (up to 2 t/h). The modular design allows for settings to be adapted to different testing requirements, which can then be analysed in detail. In this way, one can also test how different sorting techniques interact.
A new washing system
NTCP’s current sorting system takes up half of the thousand square metres of available production space. The other half is reserved for a new washing system, which will be commissioned from and installed by the plastic recycling specialist Lindner Washtech in August 2022. Lindner Washtech’s modular system allows for each individual step of the washing process to be examined and quantified in detail. Freek Van Rhijn, technical director of the NTCP says, “Soon we will be able to simulate and optimise the entire washing process for all materials. From shredding, dry washing, cold and hot washing, density separation, mechanical and thermal drying, all the way to separating with a flake sorter. We can also focus on the detergents required and the environmental impact of using more or less water. How does washing by five or ten degrees less affect energy consumption? What ends up in the waste water and how much does it cost to dispose of? With the new washing system, we can examine every single step, from sorting all the way to the final clean plastic flake.”
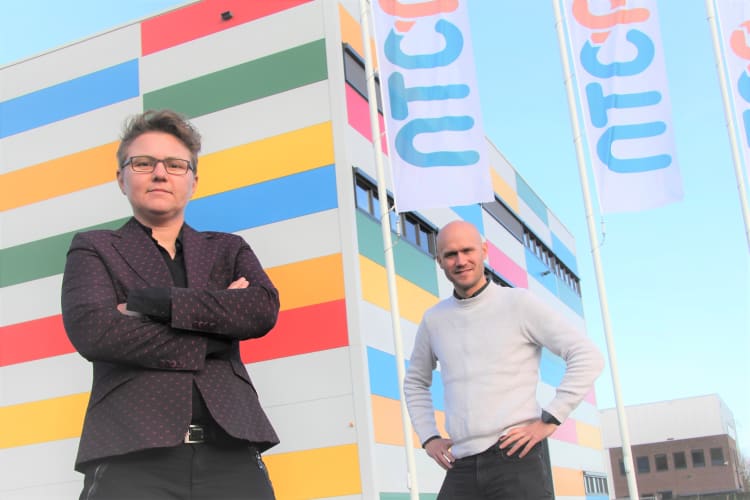