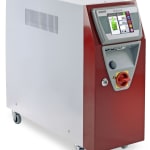
The Wittmann Group, represented by Battenfeld (Schweiz) AG and Wittmann Kunststofftechnik AG, will present its latest range of injection molding technology, automation and auxiliaries to trade visitors at the Swiss Plastics Expo from January 21 to 23, 2020 in hall 2, booth B 2041.
The main theme of the presentation at the Swiss Plastics Expo is to showcase intelligent machines with adaptive algorithms, which adjust themselves to various ambient conditions. This will be demonstrated with an all-electric EcoPower 55/350 equipped with the software packages HiQ-Flow®, HiQ-Melt and HiQ-Metering. HiQ-Flow® is a material viscosity-controlled injection control system, which compensates the effect of temperature and batch influences on material viscosity and thus ensures reliable, consistent good quality of the injection-molded parts. HiQ-Melt is a method of monitoring material quality, which enables easy detection of deviations in material quality by measuring the energy consumed in the plasticizing process. HiQ-Metering designates active closing of the check valve to ensure that precisely the necessary quantity of material is injected with every shot to achieve extreme consistency in part weights.
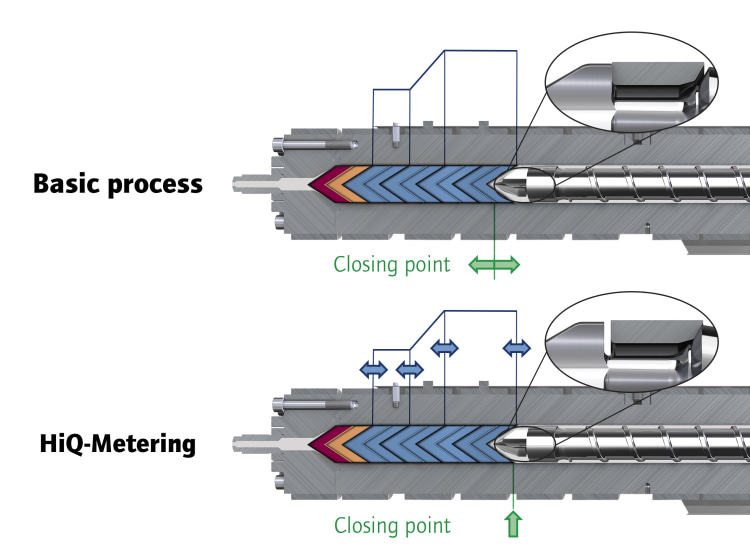
HiQ-Metering – Active closing of the check valve
A W918 robot from Wittmann, the temperature controllers of the Tempro plus D series, the gravimetric blender GRAVIMAX G14, the segmented wheel driers ATON plus H, as well as the TEMI+ MES solution, are integrated in the machine’s Unilog B8 control system via Wittmann 4.0. The electronic mold data sheet will also be used on Unilog B8. The production cell linked together via the Wittmann 4.0 router is thus able to check whether the connected auxiliaries are sufficient for the selected product data set, or if additional equipment is needed.
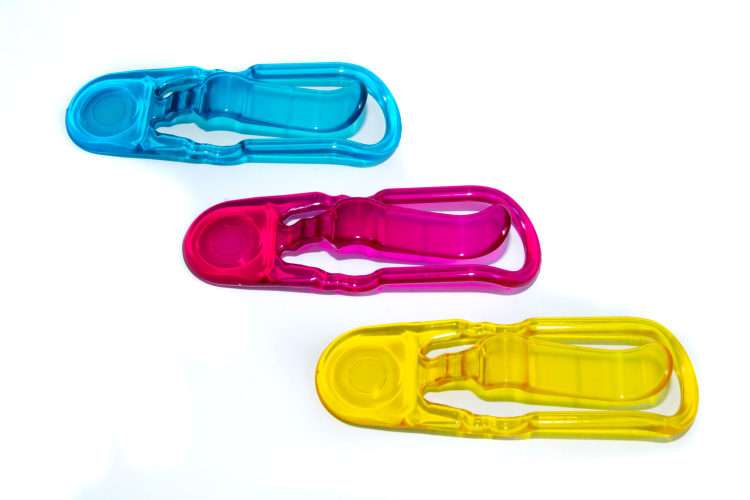
Polycarbonate clothes pegs
On the EcoPower 55/350, polycarbonate clothes pegs will be manufactured with a 4-cavity mold supplied by Lechner, Austria.
The second machine exhibited at the Swiss Plastics Expo is a MicroPower 15/10 specially designed for injection molding micro parts, equipped with a rotary table, an integrated Wittmann Scara robot W8VS2 and a camera for optical parts inspection. On this machine, micro bearing housings are manufactured from POM using a 6-cavity mold with tunnel gating supplied by Küng, Switzerland.
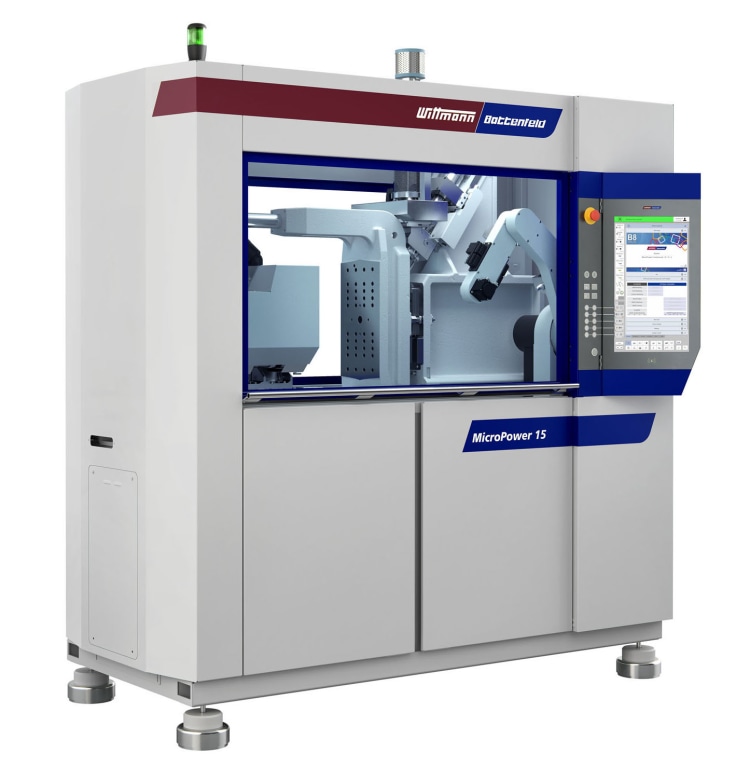
MicroPower 15/10