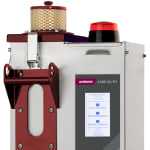
Since the Fakuma 2020 has been postponed to next year, due to the health risks caused by the SARS-CoV-2 virus, Wittmann has now decided to present the exhibits originally planned for the Fakuma together with some other interesting applications by way of product videos, and to upload them on “Virtual Fakuma”. The presentation of the videos is intended to take place primarily in personal meetings with customers, web conferences are also planned as an alternative. To present the product highlights as vividly as possible to a wide audience, the product videos will also be made available on the company’s YouTube channel. – In the following, Wittmann gives a first overview of its novelties in the areas of automation, recycling, material handling and temperature control.
Revised Wittmann robot model WX153 with many new options
For Fakuma 2020, Wittmann was presenting a completely redesigned WX153. This robot model is typically used for the automation of injection molding machines with clamping forces ranging from 500 t to 1,300 t. The predecessor version was based on the W8 pro series of appliances, which has been on the market since 2013.
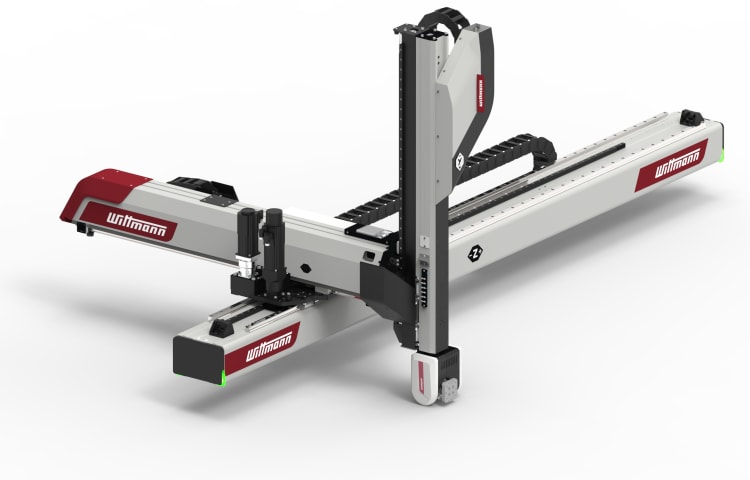
WX153 robot from Wittmann
In the mechanical redesign of the WX153 robot, special attention was paid to maximum functionality and flexible application options. So the vertical axis is now available with strokes of up to 2,600 mm. The horizontal Z-axis can be supplied with a stroke length of up to 18,000 mm. With a stroke from 4,000 mm upwards, tandem solutions involving 2 independently moving robots can be implemented as well. The control system of tandem robots also includes a joint R9 TeachBox, which is able to control up to 12 axes simultaneously. Here it is possible to choose just any combination of axes from individual robots or tandem appliances to create desired movement profiles as needed, which will subsequently run synchronously. Another new feature is the integrated compact controller housing, which contributes to even more efficient use of the carrier. The X-axis for demolding can be delivered with a stroke of 1,200 mm or 1,400 mm. In its standard configuration, the appliance offers 30 kg load capacity, which can be adjusted depending on the application. The WX153 robot comes with the Wittmann R9 control system. It offers a great variety of different functions, such as a digital twin for test runs of the robot on the screen and for error analyses, as well as SmartRemoval to minimize mold opening times.
Video assistance system in Wittmann robots with R9 control
In live sports broadcasts, slow motion replays of controversial or spectacular scenes have been common practice for a considerable time. Apart from the added entertainment value for spectators, such slow motion views also support correct decision-making by referees and can be used in training. This function is now also installed in Wittmann robots with R9 control systems.
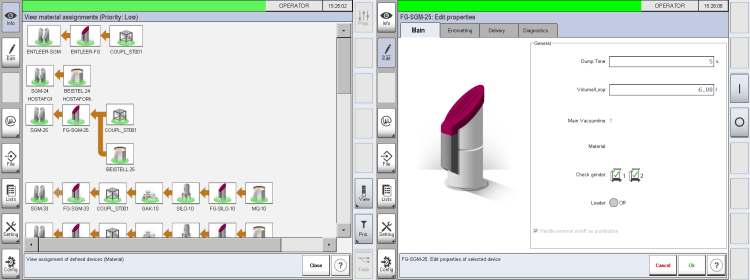
Visualizations of video assistant replay data on the R9 TeachBox.
The task of the robot’s video assistant is performed by the digital twin, which is installed in every R9 control system as standard. The digital twin is displayed directly on the TeachBox and can replay preceding sequences at any desired speed. As the digital twin has access to the configuration of the physical robot on which it is installed, it is familiar with that robot’s equipment options and is able to visualize these appropriately.
As soon as the physical robot switches into the automatic operation mode, the twin records all changes in the positions of the individual axes, the entrance/exit points, the counters and all other values relevant for the operation of the appliance. All data are recorded with a precision of 4 ms and can be traced back into the past for up to 100 seconds. In this way it is possible to access the record for any desired point in time. Another vital fact is that the teach-commands executed are saved here, too.
An example of a practical application could be the standstill of a robot for unknown reasons – with the subsequent option to retrieve a visualization of the incident on the TeachBox for fault analysis. When the robot standstill occurs, the data recording is discontinued, and the preceding 100 seconds are now available for analysis. A time controller installed on the TeachBox makes it possible to define a point in time within the displayed sequence. This controller can be shifted in both directions as desired, in order to examine in detail and repeatedly critical changes of status which have occurred.
During the analysis, the physical robot could stay defective or out of function, since only the digital twin is moved on the TeachBox, and only its status changes are displayed.
The video assistant makes it much easier to detect causes of defects and supports the operator’s efforts to prevent a repetition of similar incidents. Consequently, it contributes to increasing the uptime of every R9 robot – and thus the efficiency in production.
G-Max 13 beside-the-press granulator
The G-Max 13 completes the existing G-Max granulator series from Wittmann, which offers cutting chamber sizes ranging from 130 × 260 mm to 460 × 235 mm and engine outputs from 2.2 kW to 4 kW. The models from the G-Max series can be used for material throughputs of up to 50 kg/h on injection molding machines with up to 500 t clamping force.
The G-Max 13 granulator is suitable for in-line recycling of soft to medium hard sprue consisting of PP, PE, ABS or PU, and can be used on injection molding machines with clamping forces of up to 230 tons.
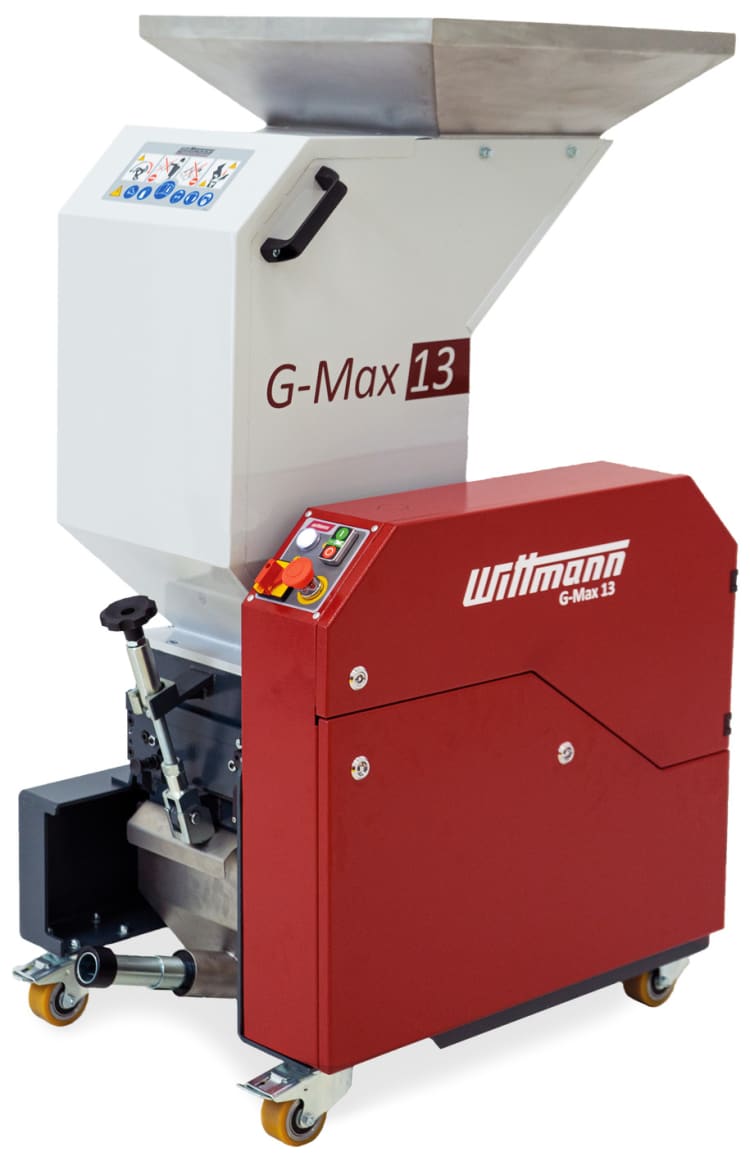
The new G-Max 13 granulator from Wittmann