The material screens of the G-Max 13 are available with screen perforation in different sizes: either 4 or 5 mm in diameter. This ensures suitability for varying materials and throughputs. The perforations in the screens have a conical shape, so that soft and sticky granulate can pass through more easily. A feature which ultimately contributes to minimizing the accumulation of material deposits in the openings. The tiltable material hopper simplifies cleaning and servicing of the appliance enormously. For instance, a screen change can be carried out without tools, and the time required for servicing is reduced to a minimum.
The granulator has an open rotor with three knives. It is designed with openings between the knives and the rotary axis to ensure unhindered ventilation of the cutting chamber. Thanks to this type of design, this model is ideally suited for grinding materials which are sensitive to heat or parts not yet completely cooled. Exchanging knives is extremely easy and comfortable.
The new G-Max 13 can handle a material throughput of up to 35 kg/h (depending on the shape of the parts/sprues, screen size and quality of material), it operates with a low noise level and is extremely energy-efficient.
G-Max 13 – technical features |
|
Cutting chamber |
247 × 284 mm |
Motor output |
3 kW |
Number of knives |
3 |
Rotor diameter |
180 mm |
Regrind bin |
13 liters |
Rotor speed |
200 rpm – 50 Hz |
Drive |
Belt drive with automatic tensioning system |
M8 network control for central material handling systems
User-friendliness and functionality of control systems are a top priority for Wittmann. With the revision of the current M7-IPC control system, the CAN-bus-based M8-IPC network control system has been introduced. It simplifies the administration of complex installations and shows a clear display of every appliance in modern design.
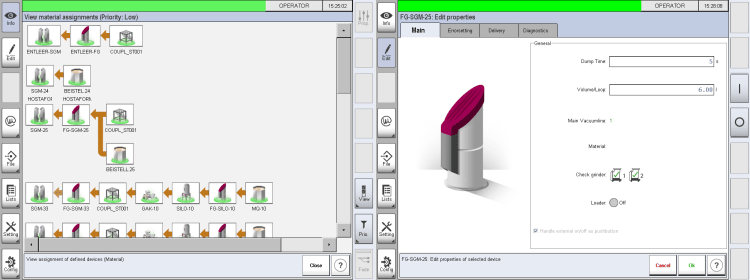
Views of the M8 screen: administration of material loaders.
A new feature is a number of freely programmable modules – or “logical devices” – which support queries, counting functions, loops and much more, to enable logical switchover and connection of outlets. To give an example: as soon as one source of material runs out, the system switches over automatically to another source. These new possibilities to define logical operations offer users an easy way to program sequences perfectly geared to each individual process.
What is more, M8 comes with a “counting” functionality: whenever a user wishes to have a certain action triggered following the execution of a fixed number of switch cycles, this is now very easy to implement.
Another new feature is coded regrind recycling. If the regrind coming from several machines is not all processed in the same way, the regrind from individual granulators can be transported unmixed into separate containers. RFID-coded materials handling devices ensure that materials are only transported if the material line is correctly connected to the granulator and to the matching container. In this way, mixing of different types of regrind is prevented.
Something often requested – and now also made possible: residual quantities of material left on the machine can be transported back to the material source. If the production is interrupted, there is a risk of dried material being left on the machine during the time of standstill, which then causes start-up problems when the production is resumed. Or it happens during a material change that left-over material on the machine is (mostly) emptied out and then disposed of. With the help of the M8-IPC control functions, such residual quantities can be “reclaimed” and re-used.
The operating status of the individual appliances catches the eye immediately thanks to the different color codes. In case of error signals it is possible to have persons responsible notified by email.
Operators can choose between several different systems to perform the tasks assigned to them quickly and faultlessly.
For this purpose, several different views are available, showing the path followed by the material – through all stations right up to the consumer, that is, up to the machine and/or to the mold.
One view is assigned to the administration of users; it enables comprehensive administration of individual users or groups of users and the appliances allocated to them.
Another special view is available to visualize the vacuum participants. Here, the material loaders, valves, vacuum and filter stations of a given vacuum line (or all vacuum lines) are depicted clearly allocated in their context. In case of emergency shut-offs with the use of replacement pumps, the automatic changeover valves and all connections that have been changed are shown to the operator.