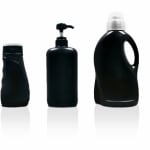
The primary target of the “Circular Economy for Plastics” is that plastics should never be found as a waste in the environment. There are different ways to achieve this, starting from the proper design of the plastic article through efficient collection and sorting of the various polymers to recycling and reintroduction into the life cycle. Additionally, the use of bio-degradable polymers offers further possibilities.
Top Fast-Moving Consumer Goods companies and plastic packaging producers representing over 20% of the global packaging market have committed to making 100% of their plastic packaging reusable, recyclable or compostable by 2025.
No doubt that color will continue to play a key role in the packaging world. But the selection of the right colorants will be crucial.
Let’s go through the various parts of the cycle and show how a pigment and polymer soluble dye producer can help the stakeholders combine the need for color and the equally important need for sustainability.
Design for recycling
Everything starts with the designer of the packaging. The task is to create packaging that is appealing, enhances the brand image, provides a differentiation and that can be properly recycled and reused as resin for new plastic products.
Depending on the recycling technology (mechanical, chemical), the choice of the colorant will be different. The designer needs to know which processing steps the article will be facing, not only for its production but also for its time after usage. This will influence the selection of the pigments. There will also be switch of polymers and changes in the composition of the packaging.
Since the brand owners have committed to incorporating significant amounts of recyclates in their new packaging articles there will be a further challenge to achieve brilliant and appealing colors.
Clariant Pigments is working on solutions to these challenges, such as faster and easier color matching with recycled resins or setting up a pigment range that can withstand various recycling loops without decomposing and remaining safe for future applications and for the working environment.
Reuse is another aspect of sustainability. In this case the colorant selection also requires a particular attention since it has to remain appealing and safe.
The color should not fade out for the product to keep its appearance even after numerous reuses. High light-and weather fastness are key criteria.
The safety aspect is even more important, especially when we talk about bottles for drinks. The pigments should not migrate into the drink after the bottle has been washed many times with hot water containing strong detergents, for instance.
Clariant’s pigment portfolio offers a wide range of solutions.
Recycling
There are three main recycling technologies:
- Mechanical recycling,
- Solvent based recycling,
- Chemical recycling (depolymerization, pyrolysis, gasification).
Whatever the process is, proper recycling starts with proper collection and sorting of the plastic waste.
In an optimal sorting center plastic is automatically sorted through different stages according to polymer types and color using Near Infra-Red (NIR) technology. It can separate the plastics according to their type, e.g. LDPE, HDPE, PP, PET, PS streams.
To work properly this technology requires a minimum amount of energy to be reflected to the sensor. It becomes a problem if the plastic part absorbs the NIR energy instead of reflecting it. The issue arises with plastics colored with a carbon black pigment. Carbon black absorbs in the NIR range which means that plastic articles colored with carbon black will not be identified during the sorting process and thus cause much trouble in the further recycling steps or end up in landfill.
Clariant has developed three colorants which can reflect in the NIR spectrum and will allow the plastics industry to still produce black articles which can be sorted properly. These grades can be used for HDPE, LDPE, PP, PET, PS, PA and PVC.
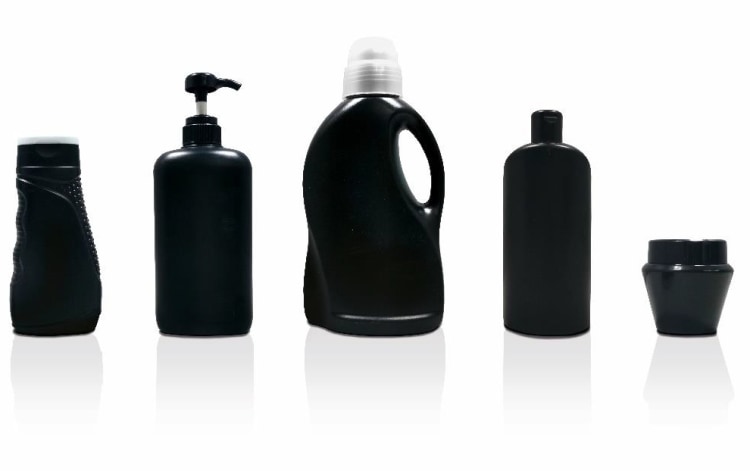