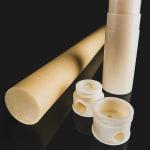
BASF has now developed Ultramid® Advanced N5H UN, a polyphthalamide (PPA) that can be manufactured into semi-finished parts by extrusion. The plastics company GEHR, Mannheim, Germany is using the new PPA to produce extruded stock shapes with a diameter of 50 millimeters. Ultramid Advanced N offers excellent mechanics at elevated temperatures due to its semi-aromatic chemical structure. It shows excellent resistance to chemicals and hydrolysis, even in aggressive environments, as well as good sliding friction properties – and all this at temperatures above 100°C. Due to its low water uptake its mechanical properties remain stable over a wide temperature range. Even in humid environments, the long-chain high-performance material shows a dimensional stability that belongs to the highest of all polyamides.
This property profile makes Ultramid Advanced N the perfect material for extruding pre-fabricated components and small assemblies but also for many applications in the automotive industry, in mechanical engineering and in kitchen appliances. During machining, the behavior of the semi-finished products lies between a polyamide and a polyoxymethylene copolymer, with steady and consistent chip formation and removal.
“GEHR is the first company to successfully use a PPA for extrusion. With its expertise in extrusion, GEHR has developed stock shapes that can be produced without any voids”, says Philipp Wenz, group head in sales of BASF’s Performance Materials division. “We can't say for certain whether it’s the world’s first semi-finished part made from polyphthalamide. The high-performance material has definitely not yet played an important role in the market for semi-finished parts. One reason for this might be that usual polyphthalamides cannot be extruded very well.” Thus Ultramid Advanced N5H closes a gap in the market between semi-finished parts made of polyetheretherketones and polyarylsulfones on the one hand and semi-finished products made from engineering plastics on the other hand. In comparison to the latter it can be used at continuous operating temperatures well above 120°C. The BASF material is also suitable for profiles other than rods.
Bernhard Grosskinsky, Head of Application Technology at GEHR, explains: “BASF’s polyphthalamide is far easier to process compared to other PPAs on the market. It gives us a wide processing window with at the same time a high melt stability. The quality of the material always remains the same so that we can maintain a stable production of our semi-finished parts. Last but not least, another advantage of BASF’s PPA: It is easy to produce finished components from the semi-finished products by post-processing.”
A wide range of applications can be manufactured from GEHR’s extruded rods: Components with very high operating temperatures and pump parts requiring exact dimensional stability are just as feasible as gear wheels, thermostat housings and sliding rails. In the automotive industry, the material is particularly suitable for components that come into contact with motor and transmission oils, coolants, acids, salts and de-icing fluids. Parts that require high sliding friction properties can be used even at high temperatures due to the material’s high impact resistance and very low wear rate.