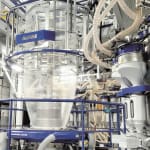
The Polish packaging manufacturer ERG S.A., headquartered in Dąbrowa Górnicza, has invested in a modern 7-layer blown film line with inline MDO (Machine Direction Orientation) from Hosokawa Alpine for the first time. The line has been in operation since August 2022 and supports the traditional company in its vision to produce only fully recyclable plastic films. In addition to the positive environmental effects, the plant has increased production capacity by 30 percent.
Hosokawa Alpine’s MDO technology is a key component in the production of high-performance mono-material films made of polyethylene. In the past, to create certain product properties, composites had to be produced from different materials that cannot be fully recycled. A more sustainable concept is packaging solutions made from pure polyethylene composites. These are in line with the principle of the circular economy, as they can be fully recycled after their original use and reused for end products without material loss. "Our vision and mission is the sustainable development and production of innovative packaging that meets the needs of our customers while minimising the negative impact on the environment," emphasises Tomasz Gwizda, commercial director of ERG. In doing so, the company can draw on 120 years of experience. Today it produces various types of films, including films made of PE composites or EVOH, fully recyclable films or full PE films. For full PE films, ERG uses the new 7-layer line with inline MDO from Hosokawa Alpine.
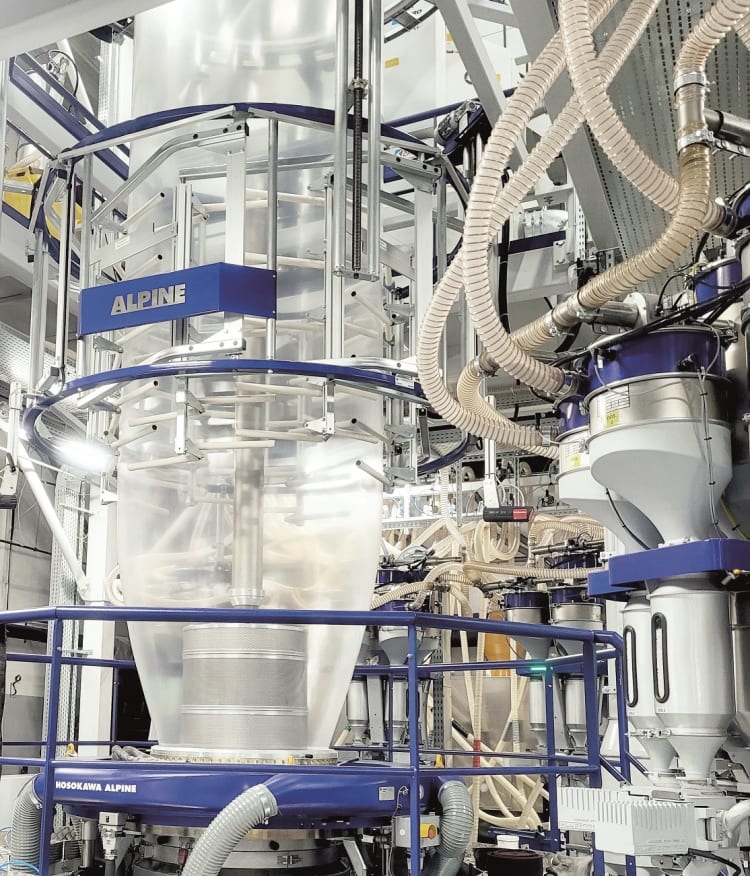
The new 7-layer line with inline MDO (Machine Direction Orientation) from Hosokawa Alpine at ERG in Poland.
Precisely fitting line design and high film quality.
"More than 100 MDOs made by us are now in use all over the world," says Richard Hausner, Sales Manager Poland in the Film Extrusion Division of Hosokawa Alpine. Together with the customers, Hosokawa Alpine designs the respective MDO blown film line precisely for the desired film production, tailored exactly to the customers’ needs. "This was also the case with ERG and this is one secret of our success. The other is the quality of the MDO films," says Hausner. It is characterised by excellent processability, optimised flatness and no hanging edges. To achieve this, Alpine’s MDOs are equipped with three unique features: TRIO technology (Trim Reduction for Inline Orientation) for best flatness and roll cylindricity, the flexible adjustment of the stretch gap to reduce neck-in, and the unique vacuum technology for best flatness and excellent process stability.The Hosokawa Alpine MDO technology is based on monoaxial stretching of blown film. The film is pulled between two rollers that rotate at different speeds. Depending on the application, the film runs over eight to twelve rollers, two of which are stretching rollers. After heating to the optimum temperature, the film is brought to the desired ratio in the stretching phase. The stretching process reduces the film thickness while improving the optical and mechanical properties. These include, for example, barrier properties, transparency or processability. "The raw material requirement can be reduced with this technology in a resource-saving way and efficiency can be increased," Hausner explains. The stresses created during stretching are reduced in the subsequent annealing phase. Finally, the film cools down and compensates for the thermal shrinkage. "Our composite films based on MDO-Full-PE films and a sealing layer made of LDPE - also in a high-barrier version for gases - meet all the requirements of a modern circular economy and are 100 per cent mechanically recyclable," says Gwizda happily.
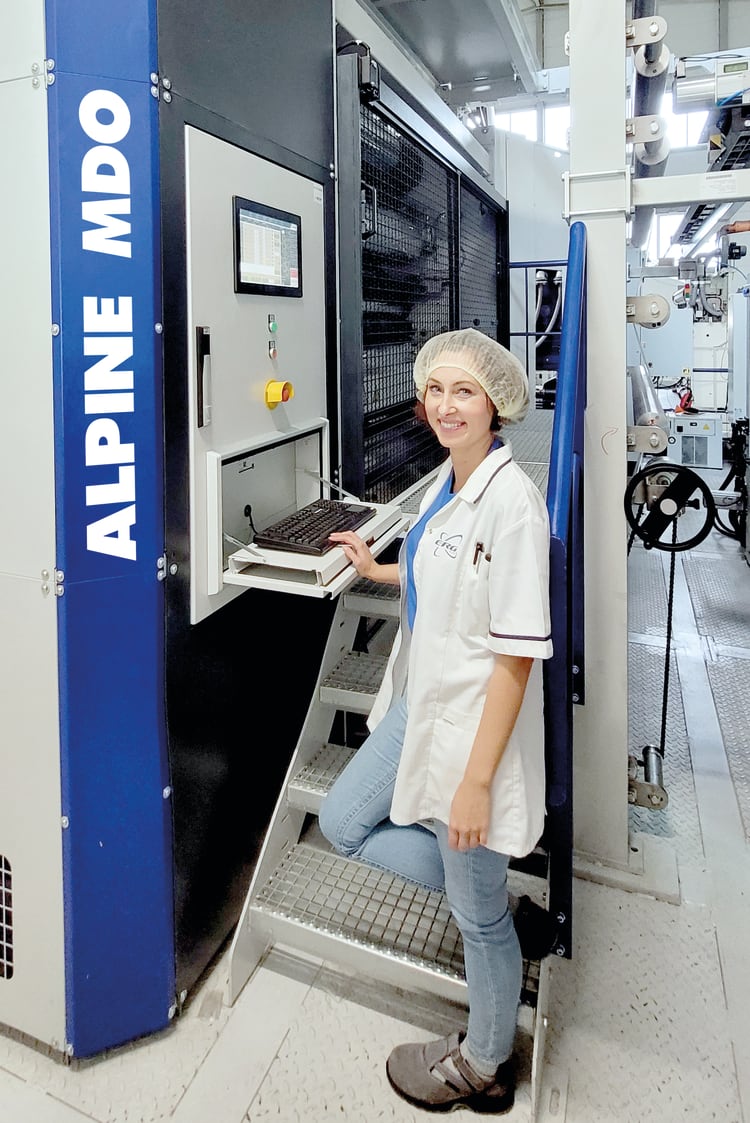
The Hosokawa Alpine MDO technology is based on monoaxial stretching of blown film. The film is pulled between two rollers that rotate at different speeds. In addition to the positive environmental effects, Hosokawa Alpine's MDO line has increased ERG's production capacity by 30 percent.
PE-MDO film replaces BOPET and BOPP films
One of ERG’s products manufactured with the MDO system is the PE-MDO film Premium. Depending on the version, it is a seven- or fourteen-layer film for printing and laminating. As a mono-material packaging and an alternative to LDPE composites with BOPET and BOPP films, it is 100 per cent recyclable. "Due to its unique mechanical properties, the film is suitable for both surface and interlayer printing in flexo, offset and digital printing," says Gwizda. In addition, the MDO technology gives the film several properties with explicit added value due to the specific arrangement of the polymer chains. Among these are higher stiffness, transparency and durability, as well as lower permeability to water vapour and gases. Depending on the choice of raw materials, MDO-PE films can be produced in different versions, which are additionally characterised by a much higher temperature resistance. They are mainly used in food packaging.
With the new MDO line from Hosokawa Alpine and its own laboratory for research and development of new film types, ERG currently sees itself as being ideally positioned to meet the challenges of current future trends. "If you want to benefit from all the advantages of MDO technology and install a future-proof plant, there is no way around Hosokawa Alpine and its more than 25 years of experience," concludes Gwizda.