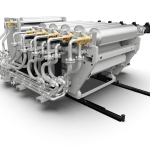
At the K 2022, a Multi-Touch roll stack stands once more at booth No. B 19 in hall 16. The concept of multiple roll nips and extended contact between the rolls and the sheet has already proved successful worldwide over a long period of time in many applications in producing high-quality, low-stress sheet and boards. As a specialty for this year, battenfeld-cincinnati is presenting a roll stack in horizontal configuration perfectly suited for sheet polished on both sides, such as mono- or multi-layer sheet for the dairy industry.
The horizontally arranged roll stack for making thin sheet from polypropylene polished on both sides, with an output of up to 1,200 kg/h and speeds of up to 120 m/min comes with several special features. The roll stack is laid out to handle sheet thicknesses ranging from 200µm to 2000µm. In order to process especially thin sheet safely, it is absolutely vital to be able to precisely control the position at which the melt first comes into contact with the rolls. Moreover, the of the knead is of paramount importance in this thickness range. The solution for this special extrusion line was to have the die positioned vertically above the roll stack, to enable the roll stack to adjust its position with a high degree of accuracy. This makes setting of the equipment extremely variable and precisely adjustable to specific needs.
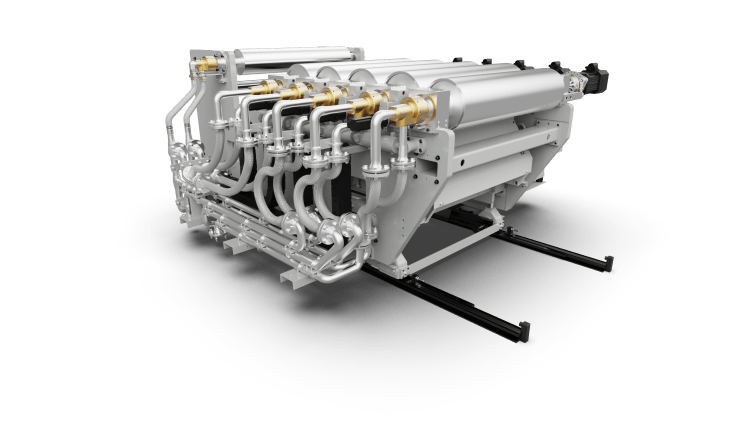
Furthermore, the roll stack is not only suitable for producing 3-layer sheet, but can also be used for laminating functional sheet. In such cases, the laminating film is fed directly into the second roll nip, welded onto the surface of the main sheet while it is still hot, and the completely laminated sheet is then cooled evenly by its long roll contact during the pre- and post-calibration phases. In this way, the polishing process inside the first roll nip is separated from the lamination process in the second nip, so that the two processes cannot influence each other. Thanks to the use of a special roll design, the sheet polished on both sides comes with extremely narrow thickness tolerances as well as minimal residual stress and optimal surface attributes.
The roll stack on display is part of a complete line, with the extruder being placed on a higher level above the roller mill. This arrangement enables the implementation of an extremely compact design which nevertheless provides easy access to all individual components of the sheet extrusion line. Moreover, the delivery hydraulics normally integrated inside the stand is mounted on the outside of the roll stack stand in this version, a significant enhancement of user friendliness and simplified servicing.