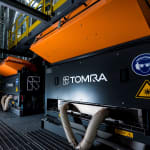
The recycling sector in Mexico is witnessing the collaboration of two companies, Tomra Recycling and Indorama Ventures Public Company Limited. Dedicated and committed to enable greater sustainability and an environmentally friendly way of production and consumption, both companies seek to promote the future of plastics recycling in Mexico by producing recycled plastic of the highest quality. In 2014, Indorama Ventures, a global chemical producer, acquired the PET recycling Plant, located in Zapopan, Jal. (Mexico). This acquisition allowed the company to pursue its strategy of expanding into high-growth regions such as Central and Latin America. Supported by Tomra Recycling’s advanced sorting machines, which effectively sort incoming PET bottles and PET flakes, the expansion of line 2 in Indorama Ventures EcoMex was concluded this year.
Indorama Ventures entered the recycling business in 2011 and operates production facilities that transform post-consumer PET bottles into flakes, rPET resins and recycled polyester yarns. "Our close, highly personal relationship with Tomra has been key to the selection of the equipment and technology, as well as the service they provided. They have worked seamlessly with us, in person and online, responding in a timely manner to meet our requirements," said Shankar Srinivasan CEO of Indorama’s Recycling Vertical.
Indorama Ventures EcoMex has a total production capacity of 42,000 tonnes per year of flake to be used in recycling process inside Indorama or with external customers. PET products offer customers a wide range of advantages: lightweight, crystal clear transparency, impact resistance, and good retention properties with 100% recyclability.
In 2014 and as part of the company’s ongoing commitment to meet the needs of its customers and contribute to environmental care efforts, Indorama Ventures Polymers Mexico started the production of FuTuRePET bottle grade resin, which consists of the flakes produced from post-consumer PET bottles at their facility. Thanks to Tomra's equipment, it has been possible to effectively separate the materials by color and material to create pure recycled materials, ready to be reused.
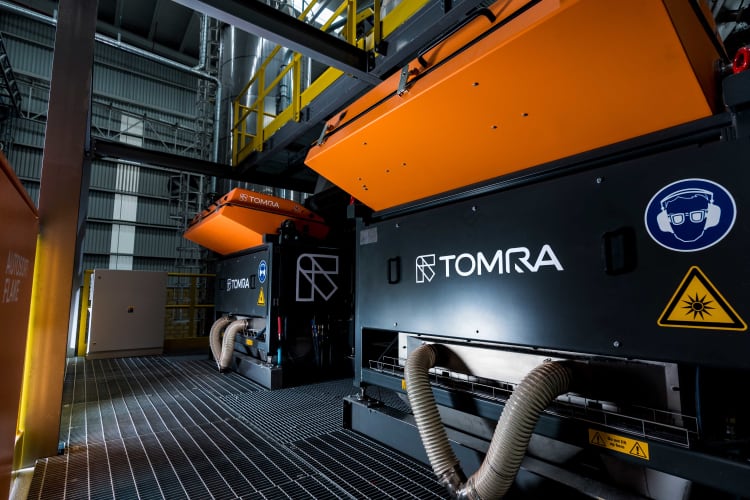
As part of its commitments adopted from the 2030 agenda for sustainable development issued from the United Nations in 2015, Indorama started installing a second PET bottle post-consumer recycling production line in 2019. The line, equipped with Tomra’s state-of-the-art sorting machines, will process 30,000 tons of PET flakes per year.
Indorama and Tomra share three main objectives to achieve this goal, which are: consolidating the production line, increasing the quality and speed of production, and reducing costs. To do so, Indorama has chosen Tomra’s sensor-based sorting machines to effectively sort the infeed material by color and material.
In a first step, two Autosort units presort incoming PET bottles obtained from landfills and collection centres primarily from central and western Mexico. The presort includes one positive and one negative sort plus a recirculation process for the false rejects from the first two machines.
Presorted materials are then washed and shredded before the respective PET flakes are further sorted and purified by two Autosort FLAKE units, which generate tonnes of flakes per year. The flakes produced are further recycled and made available as food-grade PET resin to plastics converters.
Tomra’s machinery brings a wealth of benefits from which recyclers can profit. Autosort combines leading-edge features and technologies in one machine. Compact and flexible in construction, Autosort allows for simple integration into existing and new plants. Featuring Tomra Flying Beam technology, the machine provides uniform light distribution across the entire belt width for better material detection and sorting, resulting in high performance and operational efficiency. This enables the plant to sort PET bottles with high levels of accuracy.
Autosort Flake, one of Tomra’s flake sorting machines, is the ideal solution for high-end applications where the numbers of contaminants are low, but quality demands are extremely high, such as in PET bottle to bottle recycling as done with Indorama Ventures. It offers a unique technology combination consisting of the high-resolution Flying Beam sensor, a full color camera, and a highly sensitive metal sensor to allow for sorting flakes by both color and material. Autosort Flake also achieves high throughput, leading to consistently high productivity and sorting results.
"Autosort is focused on segregating waste materials based on customer requirements. The equipment is programmed according to the required purity quality needs. The machine's high-frequency and high-speed cameras, metal detector and infrared technology determine contaminants and tonalities in order to achieve the highest degrees of purity," added Julio Barrientos, Recycling Sales Manager in Mexico at Tomra.
The combination of these outstanding technologies enables a fast and simultaneous multi-sensor evaluation of input material and precise removal of contaminants. Indorama is a success story of the reliability and performance of Tomra machinery. Apart from the technological advantages delivered, Indorama appreciates the quality of Tomra's service. "The services provided by Tomra have been personalized, either in person or virtually, always responding in a timely manner to our requirements. Their service and expertise, combined with high-tech equipment, have helped us in bringing our production to the next level. We produce high quality products and profit from substantial savings”, describes Shankar.
The collaboration of Tomra and Indorama proves to be a promising one in terms of advancing the recycling sector in Mexico. With both companies having high standards in operations, services and products, the recycling activity and innovation in this sector are greatly supported and strengthened.
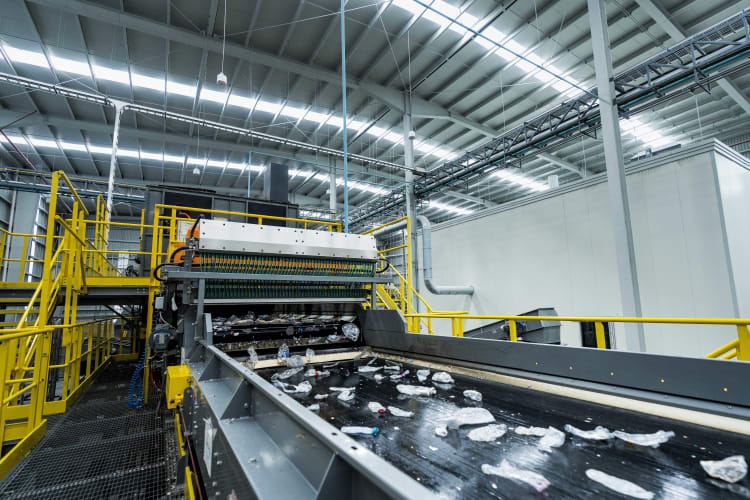