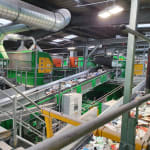
In 2019, Stadler UK Limited was appointed by Viridor as one of two main contract partners for the £15.4m upgrade of its Masons Materials Recycling Facility (MRF) near Ipswich, modernising the facility as part of a ten-year Viridor-Suffolk County Council contract renewal. Viridor runs the MRF on behalf of the Suffolk Waste Partnership.
Viridor specified Tomra Sorting Recycling’s sensor-based sorting solutions in its tender documentation for the upgrade. Having already worked together on several projects around the world, Stadler and Tomra worked in close collaboration from the earliest stages of the tender enquiry to ensure the plant and equipment met Viridor’s specific requirements.
By investing heavily in the plant upgrade, Viridor has been able to transform its operations, increasing capacity from 65,000tpa to 75,000tpa (equivalent to 17 tonnes per hour). The plant is now operating at full capacity and at optimum processing levels. Output quality has also improved considerably thanks to the new Tomra equipment installed during the upgrade.
Masons’s infeed material is comingled dry mixed recyclables (not including glass) from Suffolk County Council. The material is first processed using brand new mechanical separation equipment, including a dosing drum, a Stadler PPK ballistic separator, a screening drum, Stadler STT 2000 ballistic separators, overband magnets and eddy current separators. Following mechanical separation, the material (apart from fibre) then goes through an air separation process before arriving at the newly installed Tomra Autosort optical sensor-based sorting units.
Prior to the upgrade, three Tomra optical sorters were in place at the MRF. These were replaced by 11 new Tomra Autosort units. As one of the existing units was only four years old, Tomra simply uploaded the latest software.
The units have been programmed to sort and recover mixed fibre (cardboard, mixed paper and newspapers and pamphlets), and to sort mixed plastics by polymer into high purity single stream plastics (PET, HDPE, hard plastics, film, pots, tubs and trays).
The Autosort system brings together the very latest in Tomra’s technologies to deliver advanced accuracy of complex sorting tasks at high throughput rates. Capable of separating materials which are difficult or even impossible to separate using conventional technologies, Autosort delivers consistently high-performance sorting accuracy across all target fractions – even in the most complex of applications.
Once the MRF’s infeed material at has been processed by the relevant Autosort units, it is given a final quality control check before being baled ready for transportation to end customers, all of whom are UK-based. Any material that is left once all the target fractions have been recovered is sent for energy recovery or to landfill.
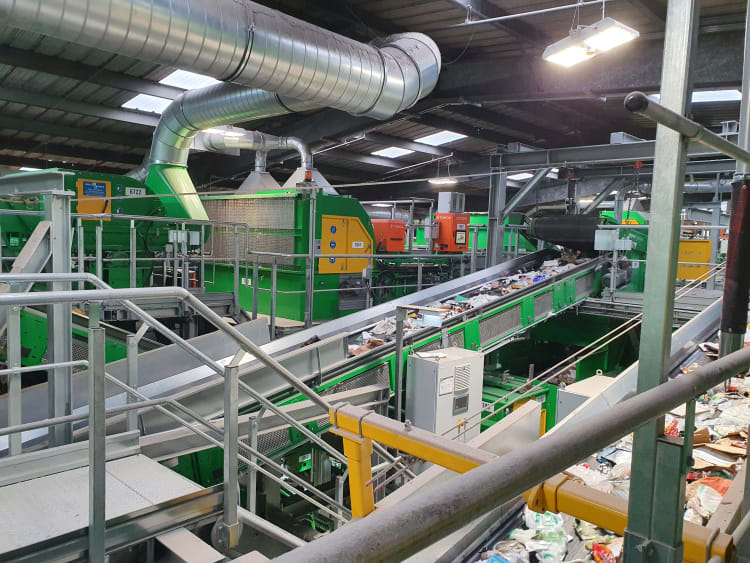