With the new mechanical and sensor-based equipment in place, Viridor is now reaping a number of operational benefits, including:
- Increased throughput - the plant can cope with a higher tonnage of infeed material (10,000 additional tonnes per annum)
- Market-leading purity of target fractions, eg 98.5% purity on newspapers and pamphlets and 95%+ for polymers such as PET, HDPE and mixed plastics
- Cost efficiencies resulting from the plant running at full capacity
- Reduced risk of plant downtime
- Futureproof solutions – the equipment is designed with ever-changing market needs in mind and can be reprogrammed to cope with changes in the infeed material stream
- Cost savings derived from sorting PET and HDPE – previously this material was sent to Viridor Rochester for reprocessing but now it can be reprocessed on-site, cutting the carbon footprint and saving on reprocessing costs
Steven Walsh, Sales Engineer at Tomra Sorting Recycling, comments: “We were delighted to work with Stadler on this project, having already worked with them on a number of other projects nationally and internationally. Prior to the refurb, this Viridor site could only sort mixed plastics for further processing at the Rochester PRF and it was extremely manual sorting focused, with hand sorting used for all cardboard and refined paper grades. Now though, Masons is among the most highly automated plants in the UK and by integrating Tomra equipment and benefitting from Tomra’s technical expertise, Viridor can capture superior quality materials ready to feed back into the circular economy.”
Benjamin Eule, Director at Stadler UK Limited, adds: “Our role was to decommission the existing plant and supply and install a full turnkey solution for the newly upgraded plant. It was one of the quickest turnarounds we’ve ever worked on. It only took around three months from the initial discussion to signing contracts and then, once contracts were signed, we were on-site five months later to undertake the installation. It took two weeks to decommission the plant and everything was brand new other than one Tomra optical sorter which Tomra simply uploaded the latest software onto as it was only a few years old. The installation – including demolition of the old equipment – took 80 days in total. We installed new steel work, conveyors and all electrical components required for the process. We also managed both the cold and hot commissioning processes.”
Viridor Recycling Director, Derek Edwards, said: “This is by far the largest investment in a UK MRF in recent years. Viridor is heavily focused on developing opportunities to put quality recycling materials back into the economy where they belong. This starts with viewing waste as a resource, rather than rubbish, and, thanks to Suffolk’s commitment to recycling, and our investment in the Masons MRF, we are well positioned to make the most of the county’s recycling opportunities and to sell that material onto UK-based end customers.”
Mr Edwards added: “The Masons investment plan has been specifically designed not only to achieve greater capacity but to match its output quality with market requirements. The plant has the same infeed material as before, but can now cope with an additional 10,000 tonnes of material per annum. We’re delighted with the performance of the plant and its equipment since the upgrade was completed.”
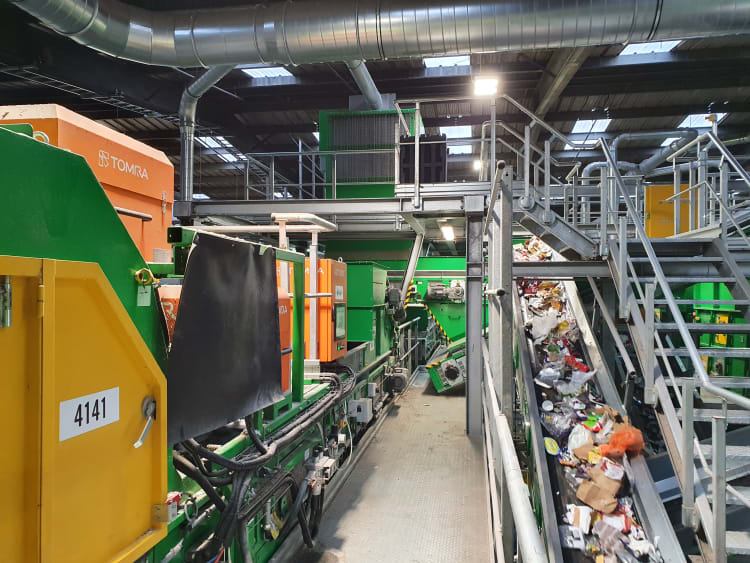