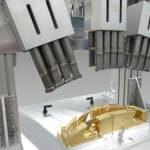
Ultrasonic welding for joining of thermoplastic materials is a widely established joining method in the automotive industry. Applications range from interior (side door trims, center console) to engine compartment (cylinder head cover, engine covers) through to lighting, such as tail-lamp units of daytime running lights.
Ultrasonics allows for gentle component handling
The conventional joining technologies reach their limits with asymmetrical components. One limit may be uneven temperature distribution during i.e. mirror-imaged welding. Some points may become too hot and produce threads; other points may remain cold and are not able to bond homogeneously. With vibration welding additional space is required so that the joining zone becomes significantly larger. A large amount of molten material is produced, which may be projected out of the welding spot. Ultrasonic tools vibrate with a frequency of 20.000 Hz or more. In case of complex, asymmetrical parts, ultrasonics may be subject to physical limits. However, if the weld tool, i.e. the Sonotrode, is correctly dimensioned by using Finite-Element-Method (FEM) and applies the vibrations correctly, ultrasonics represents a number of advantages:
- Sensitive component surfaces are treated gently
- Targeted energy input protects reflectors and LEDs
- 3-D shapes are realized more easily
- Short weld cycles between 100 and 300 milliseconds
- Smaller machine footprint compared to other joining processes