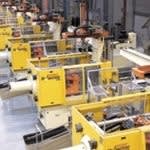
The product line will feature two performance levels, each of which will deliver industry-leading cycle times for their target applications, together with the highest levels of reliability, repeatability and part quality. NPE will serve as the global introduction for the latest generation of the product line with a HyCAP system running.
The HyCAP 300 system at NPE 2012 will be producing a 0.95 gram 26/22 lightweight water closure at a 2.2 second cycle using a 96-cavity KTW beverage closure mold. At NPE 2009, Husky first launched the HyCAP product line with a HyCAP 300, 72-cavity system running a similar application at a 2.4 second cycle. This 45% productivity improvement was made possible with a number of system-level enhancements.
“Part of our beverage packaging portfolio, our new HyCAP closure manufacturing systems are now developed as completely integrated solutions. This approach has enabled us to identify and eliminate waste throughout the production process,” said Jeff MacDonald, Vice-President, Marketing. “In doing so, we have been able to strengthen each of the discrete products such as the machine, mold, hot runner and controller as well.”
HyCAP HPP is the world’s fastest closure system and represents a revolutionary step forward in beverage closure manufacturing.
Advantages of the new HyCAP system include direct drive technology which provides improved plasticizing speed and control resulting in improved shot-to-shot repeatability and better quality parts. To maximize performance, elements of the system such as the plasticizing screw and check valve have been specifically adapted to suit the characteristics of the direct drive technology. Enhancements on the clamp include the electrification of the clamp lock function to improve efficiency and cycle potential. The new HyCAP system also features a single interface for central control of the entire system, including hot runner temperature control and auxiliary equipment.
With the addition of closure moldmaker KTW in 2011, Husky became the closure industry’s only provider of complete injection molding systems including machine, mold, hot runner, temperature controller and process and productivity software. By supplying the entire system Husky is able to provide complete melt stream control, resulting in increased productivity, less waste and improved part quality.
The latest HyCAP system has benefitted significantly from the combined capabilities of Husky and KTW and features an innovative new mold concept. The new mold design offers cycle time improvements and quick and easy maintenance in order to maximize uptime. The mold also incorporates specific features to provide ease of set-up and mold longevity while eliminating the need for sensors to monitor sensitive components.
Husky has greatly improved ease-of-use with the new systems, which include its SmartStart and SmartStop features for faster and easier startup and shutdown. Husky’s Mold ID feature provides further ease-of-use benefits by improving integration between machine and mold to allow access to specific mold setup and maintenance information.
With the latest generation of Polaris Control, the new HyCAP systems also offer the highest level of precision and repeatability thereby enabling a greater degree of fine tuning, particularly benefiting faster cycling lightweight applications.