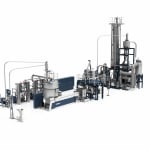
With newly developed Vacunite bottle-to-bottle technology, Austrian recycling machine manufacturer Erema redefines the benchmark for performance in bottle-to-bottle recycling: highly efficient decontamination, best colour values, top IV stability, low energy consumption during the entire process and the compact design meet even the highest demands in the production of food-grade rPET pellets.
This is made possible by the intelligent combination of Vacurema technology and vacuum-assisted Solid State Polycondensation (SSP) to create a process in which all thermal process steps are performed in a nitrogen and/or vacuum atmosphere. Vacunite is the answer to the challenges facing PET recycling, because in order to be approved for contact with food, recycled PET plastics must meet increasingly stringent quality criteria. At the same time, the demand for high-quality recycled pellets is increasing because legal requirements and voluntary commitments of leading brand manufacturers demand a higher use of recycled material in the end products. Although this development increases the overall collection rate, it also reduces the quality of the material to be recycled, as the collected material inevitably has a higher proportion of inhomogeneous components. "Recycling plants have to therefore produce better output material despite a reduction in input quality," says Christoph Woess, Business Development Manager for the Bottle Division at Erema.
The best technologies in one plant
The Vacunite process is based on the combination of Vacurema technology - which has been proven over the past 20 years and has been further developed for this application - together with newly patented vacuum-assisted Solid State Polycondensation (SSP), which Polymetrix developed for Erema especially for this demanding application. What makes this combination so special is that all thermal process stages take place in nitrogen and/or vacuum atmosphere, largely eliminating undesirable flake and pellet discoloration and reliably removing additives which could lead to unfavourable reactions in the melt. Another benefit of Vacunite: the nitrogen used in the SSP is cleaned and can be fed back into the previous processing stage so that nitrogen consumption is reduced as a result. To increase the transparency of the preforms, the pellets are dedusted again before filling.
Compact and cost effective
Vacunite is special not only because of the exceptional quality of the output material. Overall, the technology requires 40 percent fewer components, making the plant much more compact at the same time as consuming up to 36 percent less energy than comparable systems on the market. "With Vacunite we offer our bottle-to-bottle customers a new technology which sets new standards at all levels from technical performance to recyclate quality," says Christoph Wöss. The end product is rPET pellets of unique quality which, in terms of food contact compliance, significantly exceed both the current legal requirements and the even higher requirements of leading brand owners. With these advantages, Vacunite also impressed RCS Plastics GmbH. "This recycling technology enables us to take the next step towards closing the PET loop and producing food contact compliant rPET in the future. Sustainability and environmentally friendly use of resources are the principles of our corporate philosophy, which is why choosing this recycling technology was an easy decision for us to make. With Erema, we have an experienced and strong partner at our side for expanding our product range," says Alexander Rimmer, Sales Manager at RCS, explaining the decision to go for the new bottle-to-bottle process.