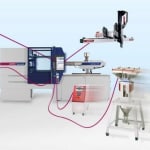
A technological prerequisite for Industry 4.0 is intelligent digital networking of machines, peripherals and sensors, to enable communication of all participants via the “Internet of Things”. The final goal of these efforts in the area of digitization is the improvement of corporate efficiency through intelligent industrial systems, which optimize themselves automatically as far as possible, through more flexible production methods and improved quality analysis.
While the German Engineering Federation VDMA has launched some very promising initiatives towards standardization of data communication between the various manufacturers, the need for the appropriate standardization in the area of networking and addressing of network participants is realized only slowly by the manufacturers of machines and appliances. The relevant problem for injection molders is that some of the additional participants now arriving on the Internet of Things are mobile units which simultaneously fulfill location-dependent functions. While it makes no difference for a network addressing where, for example, a temperature controller or mobile dryer is located physically in the production hall, this information is absolutely vital for data acquisition and analysis. A wrong allocation of peripheral appliances to processing machines – and consequently a faulty visualization of production cells – would defeat the purpose of any kind of data acquisition and analysis from the very beginning.
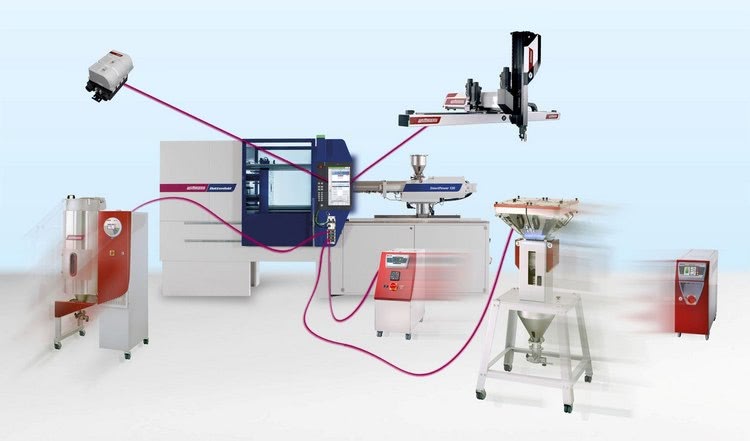
Highest flexibility: WITTMANN 4.0 allows for simple plugging and unplugging of peripheral equipment via the special switch at the processing machine.
Pioneering solution WITTMANN 4.0
The WITTMANN Group’s answer to this task is WITTMANN 4.0. With WITTMANN 4.0, not only the processing machine can be operated via the UNILOG B8 injection molding machine control system from WITTMANN BATTENFELD, but also the WITTMANN robots (with R8.3 or new R9 control) and WITTMANN peripheral appliances (with net8 control) networked with it. This enables intelligent, appliance-specific interaction between the individual appliances. Moreover, WITTMANN 4.0 allows the transmission of settings and process parameters of all appliances connected to a superordinate ERP or MES system. In the WITTMANN 4.0 system, it is not necessary at all for the MES/ERP system to address the existing physical appliances individually, but rather - fully in line with the Industry 4.0 principle - only the cyber-physical models of the participants which represent the actual appliances in a given production cell.
Simple and flexible
The unbeatable advantage of this system is that the MES system – or, in other words, the operators of the MES system, are not required to deal with any individual parts of the production cell. It is definitely not necessary to continuously make new settings in order to define precisely which appliances form a production cell at a given point in time. In contrast to most other necessary actions, this task could only be accomplished by means of manual adjustments, would thus cause an overwhelming organizational effort, which would be extremely error-prone into the bargain. After all, injection molding production requires that production cells must be formed depending on requirements placed on the mold and on the parts. So high flexibility is a must.