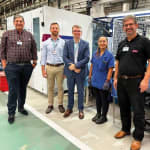
In Brazil, the Mueller/Tecnoplast group of companies ranks among the pioneers in plastics injection molding. As a longstanding partner of the country’s wellknown major automobile manufacturers, Mueller/Tecnoplast faces the daily challenge to combine firstrate quality with maximum efficiency. The technological means to meet this challenge come from injection molding solution partner Wittmann.
Two large, black injection-molded parts are what Alexandre Ramos, Director of Mueller/Tecnoplast, presents to us on the factory tour during our visit in São Paulo City. The larger of the two has just come off the clock out band from a MacroPower 650 injection molding machine. They form a glove compartment with its lid, which the Mueller division is producing for the Toyota plant in Sorocaba, just 100 kilome-ters away.
These two parts are typical examples of the company’s product range. Mueller/Tecnoplast produces parts almost exclusively destined for the automobile industry. These include many large components, such as glove compartments or, for example, fender liners and mudguards. Here, the MacroPower from Wittmann is the preferred machine model.
As Ramos explains, injection molding of glove boxes and their lids places extremely high demands on precision and surface quality: "These two parts are joined together by vibration welding. To get a good weld seam, their geometries must be perfectly matched." In this case, "good" does not just mean that the weld seam looks clean, but above all that it lasts for a long time, even when the vehicle achieves a long service life and is subjected to vibrations caused by rough roads.
Perfectly reproducible surfaces
With its extremely accurate servo-hydraulic movements and highly consistent injection processes, the MacroPower 650 makes the most of its strengths in producing these parts. Especially combined with Flowcon plus, the intelligent water flow regulator from Wittmann This device controls all cooling circuits and detects any disruptive factors such as blocked cooling channels or flow quantity fluctuations. Via proportional valves, the system then automatically compensates these irregularities during ongoing production, accurately down to the tenth. In this way, the temperature remains evenly distributed inside the mold. The result is a very high consistency in quality. "This task could not be accomplished manually, since variations in temperature control conditions only rarely show an immediate effect," explains Marcos Cardenal of Wittmann Battenfeld do Brasil. "But with this intelligent assistance system, Mueller/Tecnoplast can intervene before scrap is produced and thus save both raw material and energy."
The high reproducibility of the surfaces is so very important, because these are visible components required to match precisely the look of the dashboards, which are produced elsewhere. "When it comes to color and gloss, we have zero tolerance", says Ramos.
It was six years ago when Mueller received its first order from Toyota to produce glove compartments. Meanwhile, the processor has become the sole supplier of this interior component for all Toyota models manufactured in Brazil. "We have never had any discussions about quality issues over all these years", says Ramos. "The glove compartments are really a success story." One of many - for the corporate his-tory of Mueller/Tecnoplast is closely linked to the development of the automotive industry in Brazil.
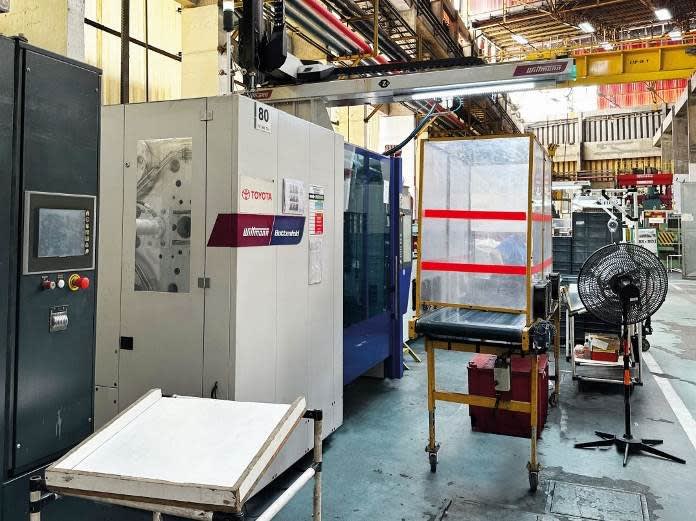
A pioneer in plastics injection molding
"Mueller and Tecnoplast are pioneers in plastics injection molding in Brazil. During the early 1950s, these companies were the first to supply the rapidly developing automobile industry in this country with plastic parts", reports Alexandre Ramos, who has had a hand himself in shaping the company’s history for the last 25 years. For a long time as Sales and Purchasing Manager, before he was appointed Director of today’s companies by the owners in 2018.
Established in 1937 by Dr. Fritz Jacob, a German emigrant, the company first made a name for itself with household goods, manufactured primarily from metallic materials at the time. In the mid-twentieth century, the new polymeric materials provided new opportunities and extended the product portfolio, thus shifting the focus of the industry. Now they can look back on decades of cooperation with partners such as Ford, Volkswagen, Scania Latin America and Toyota.
Automotive lighting opens up new perspectives
Detecting and making use of new opportunities - this virtue is firmly anchored in the DNA of Mueller/Tecnoplast. A business segment still in the making is automotive lighting, with good growth potential due to the increasing commitment of Japanese automobile manufacturers in South America. For several years now, Japanese companies have been creating a considerable stir in the market. New demands, but also more automotive suppliers are coming into the country. But even though competition is increasing, Alexandre Ramos sees this as a positive development. "I don’t intend to be the only one here, I’d rather be part of a strong production chain. After all, as the Director I’m not only responsible for the company and its associates. It is very important for me to contribute to the further advancement of our country and our society as well."
Headlights, rear lights, reflectors, lenses and light guides are less and less often im-ported, but increasingly produced locally. Tecnoplast has established another mainstay for the group of companies with these product lines. Both polycarbonate and PMMA are being processed. "For this purpose, we need the best injection molding technology", says Ramos.