Material-friendly plasticizing
With this new business segment, the first SmartPower injection molding machines, also from Wittmann, were added to the machinery. But the MacroPower machines, long proven in the company, are in use here as well. Vehicle lighting has now become a design element. In some cases, very long light guides are needed - a trend which increases the of molds.
To combine first-class optical quality with processing efficiency, Wittmann deliv-ered the SmartPower and MacroPower machines destined for the lighting business segment with Optimelt low-compression screws specially developed for this field of application. "Optimelt screws ensure a gentle plasticizing process to preserve the material undamaged", says Cássio Luis Saltori, Managing Director of Wittmann Battenfeld do Brasil. "Even in the event of brief production interruptions, ongoing production can be continued without any risk of startup scrap."
On course towards CO2-neutrality
A total of 54 injection molding machines are standing on the production floor of Mueller and Tecnoplast in São Paulo. Most of these have come from Wittmann, or Wittmann Battenfeld, as the Wittmann Group’s injection molding machine division was called until recently. As an overall system supplier, at Mueller/Tecnoplast, Wittmann is responsible for the entire equipment, including injection molding machines as well as automation and auxiliaries, ranging from granulate feeding devices right up to granulators for inline grinding and recycling of sprue. "For us, Wittmann is an important contributor to our high competitiveness", Alexandre Ramos emphas. And this concerns not only quality standards but also efficiency, which is due to several different factors.
One of these is the high area productivity provided by the MacroPower machines. Compared to large machines of other brands, the two-platen machines from Wittmann with their generously dimensioned mold platens take up only modest amounts of space. "In this way, more machines fit into the hall", Ramos concludes. "Here we are not in an industrial zone, but in the middle of a city, where industrial properties are very expensive. Compact machines and production cells mean that we can continue to grow for quite a while without having to extend our building."
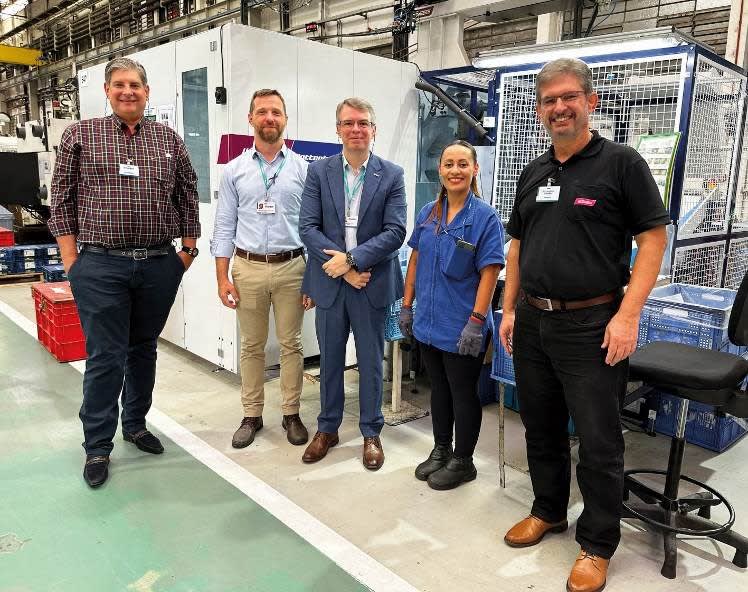
Quite apart from this, sustainability is gaining more and more significance and can be improved by way of material and energy efficiency. In São Paulo, material and energy consumptions are recorded, analyzed and optimized systematically. For this purpose, the machines already deliver a lot of valuable data today. "We can see that the Wittmann machines consume very little energy compared to other machines in our plant", says Ramos. To collect even more specific data in future and to be able to evaluate these more easily, the Group is currently installing software solutions from Wittmann Digital, such as the TEMI+ MES.
The automobile industry drives its suppliers at high speed towards CO2 neutrality. With Toyota, for example, Mueller has signed a joint commitment to that effect. The individual actions to be taken go beyond injection molding production. For instance, transport packaging for both molded parts and raw materials is being minimized more and more and reused wherever possible. Milk run optimization is also underway.
Always quickly on site
"The Wittmann machines make work very easy for our technical staff", says Alex-andre Ramos, meaning not only the robust design of the machines with clever features for easy maintenance and servicing. The manager is thinking primarily about the technical support the companies receive locally in São Paulo. Wittmann Battenfeld do Brasil is only an hour’s drive from the Mueller/Tecnoplast production plant. "We can always get help very quickly", says Ramos. "This is a great incentive for us to choose Wittmann again and again for any new projects."
The companies Mueller, Tecnoplast and Wittmann are linked by a long-standing, very close partnership - and one that goes beyond the borders of Brazil, according to Ramos. "Michael Wittmann welcomes me just as cordially whenever I am in Aus-tria, as Marcos and Cássio do here in Brazil. We keep in close contact with the corporate headquarters concerning technical matters, too. Our projects and issues are known there, and I know that the management in Austria is solidly backing its team in Brazil.That gives me a very good, secure feeling."
To make sure that his own production staff can fully exploit the potential of Wittmann technologies, Alexandre Ramos sends them regularly to training courses. Of course, to the training center at the local Wittmann subsidiary close by, but also to Kottingbrunn in Austria. "For our associates, it is very exciting to visit the machine manufacturing plant. They learn an enormous amount from the Wittmann training sessions and thus always remain up to date. This is an important method to motivate our teams. So, the trip to Austria pays off."