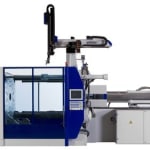
Innovative strength combined with sustainability for optimal customer benefit – these are the decisive strengths on which Wittmann Battenfeld’s success is based. At this year’s Fakuma, too, the machine manufacturer will draw the public’s attention with innovative new products.
The MacroPower 650 and the EcoPower 300 will be presented for the first time at the Fakuma 2011. This means an extension of the successful machine series of the PowerSeries – down to a smaller size in the case of the large machine, and up to a higher clamping force range for the all-electric machine from Wittmann Battenfeld. As a result, the MacroPower is now available with clamping forces ranging from 650 to 1.000 t, the EcoPower from 55 to 300 t. Modular, compact design, energy-efficiency, an open structure for quick mold change and high precision are the distinctive features of the PowerSeries.
At the Fakuma, a fitting for a clamping device with a part weight of 130 g will be produced from PP on an EcoPower 300 with a mold supplied by the IFW group. The cycle time including robot operation is 30 seconds, if the mold-maker’s special XCS cooling system is used, or 35 seconds with standard cooling. The parts are removed and deposited on a conveyor belt by a Wittmann W821 robot. In addition to high precision, the EcoPower also demonstrates its extreme energy-efficiency here with a more than 60% cut in energy consumption compared to a modern standard hydraulic machine.
On a MacroPower 650/5100 with servo drive, an intake duct for the automotive industry will be manufactured with a tandem mold supplied by Coko, Bad Salzuflen / Germany. Parts quality is ensured by SKZ online thermography. Any deviations in part dimensions caused by temperature or material fluctuations are compensated by closed-loop correction of the mold temperature.
Online thermography is a process developed in cooperation with the South German Plastics Center SKZ Wurzburg, which is exclusively marketed and distributed by Wittmann worldwide. This proves once more the “one-stop shop” competence of the wittmann group for machines, automation and temperature control. On the exhibit, a Wittmann W843 linear robot presents the parts to the camera in several different positions immediately after demolding.
The evaluation is displayed on a monitor, any deviations from the release status are visualized and calculated according to segments for the connected Wittman Flowcon flow regulator. This ensures that any temperature adjustments that may be necessary are effected in real time.
The third machine model of the successful PowerSeries, the MicroPower, which has been specially designed for high-precision injection molding of nano and micro parts, will also be on display at the Fakuma. The production of a micro part on a MicroPower 15/10 will be shown. The parts are removed by an integrated W8VS2 Wittmann Scara robot and passed on to a camera integrated in the production cell and in the machine’s control system for quality inspection.
The parts are subsequently separated according to cavities and stacked in a stacking module. In addition to the robot, a Wittmann material dryer, a temperature controller and a material feeding device are also integrated in the machine and the UNILOG B6 control system, to make up a complete production cell.